A brief introduction to Galvanized and Hot Dip Galvanized
Galvanized materials differ from their hot dip galvanized counterparts by having an even, polished surface finish, while hot sip galvanized ones may feature rough surfaces. Galvanization is the process used to protect metal surfaces from corrosion. Once galvanization has been completed using standard methods we refer to it as having been “galvanized”, while for hot dip applications, it would be more accurate to call it has been “hot dip galvanized surface”.
Brief overview of galvanization
Galvanization is a method used to protect metallic materials from corrosion by applying a layer of zinc on its exterior surface. This process has become widespread across industries like automotive, construction, electrical marine, and electrical. Submersion into a molten zinc bath precedes the application of zinc-rich paint powder coating.
Galvanization involves bonding zinc to metal to form an insulating coating that protects it from elements that contribute to corrosion, such as oxygen, moisture, and chemicals. Galvanizing not only protects from corrosion but offers additional advantages like greater durability, a more appealing appearance, and increased weathering and abrasion resistance.
Galvanized coatings are widely admired for their remarkable corrosion resistance, even under harsh environmental conditions. Their zinc composition acts as a sacrifice layer which means that when broken or damaged patches of the zinc surface fail, corrosion occurs first in its place instead of anywhere beneath. This ensures a longer lifespan for any metal object covered with it.
Galvanization has become an integral component of many industries and applications, including pipelines, steel structures fences cables electrical conduits automobile components, and many others. Galvanizing is an economical yet effective means of protecting metals to allow long-term usage across industries.
Galvanization is an essential process that plays an invaluable role in protecting metal items from corrosion while increasing durability and decreasing costs associated with repairs or replacement.
Importance of galvanization in various industries
Galvanization holds significant importance in various industries due to its numerous benefits and protective properties.
Here are some key reasons why galvanization is essential in different sectors:
Construction Industry:
Structural Integrity: Galvanized steel is widely employed in construction due to its durability and strength, offering structural integrity for bridges, structures, and other infrastructures. Furthermore, this ensures the long-term stability of those Involved.
Corrosion Resistance: Galvanization provides corrosion resistance and protects iron and steel construction components used in construction from exposure to chemicals, moisture, and environmental elements that cause them to rust over time.
Cost savings: Zinc coatings offer cost-cutting benefits by stopping erosion and prolonging their lifespan, thus decreasing maintenance and replacement expenses associated with corrosion-damaged structures and prolonging their service lives.
2. Automotive Industry:
Rust prevention: Galvanized coats applied to automobile parts can protect them against corrosion and rust caused by road salt, moisture, and weather extremes.
Improved Safety: Galvanized steel parts such as frame frames for the body, chassis, and exhaust components improve both safety and crashworthiness.
Aesthetic Attractiveness: Galvanized coatings may be used as decorative finishes on automobile parts to give them an aesthetic and durable aesthetic appeal.
3. Electrical Industries:
Corrosion Protection: Galvanized Steel is widely utilized for electrical conduit enclosures and cable trays to safeguard electrical wiring and components against corrosion, ensuring reliability in electrical connections.
Fire Resistance: Galvanized coatings are fire-resistant, making them suitable for electrical applications where security is a top priority.
Longevity: Galvanization extends the lifespan of electrical devices by protecting against corrosion while keeping equipment operational.
4. Marine Industry:
Corrosion Resistance: Galvanized coatings provide vital corrosion protection in the marine industry, shielding vessels, structures, and equipment from saltwater corrosion and marine environments.
Extended Service Life: Galvanization is an excellent way to strengthen offshore platforms, ships, and piers as well as various marine constructions against harsh marine environments while increasing their durability in extreme marine conditions.
Cost Efficiency: Galvanized coatings provide significant cost-cutting measures in maintenance, repair, and restoration costs associated with marine structures that have become corroded over time while providing long-term cost savings.
Galvanization serves an invaluable purpose across various industries by providing resistance to corrosion, increasing material durability, decreasing maintenance costs, and prolonging the lifespan of metal parts and structures. Galvanization offers an economical option that protects assets while assuring reliability and quality in various applications.
Galvanized Coating
Galvanized coatings (commonly referred to as galvanization) are a protective finish applied to metal surfaces like iron or steel to stop corrosion and improve their endurance. To apply galvanization coatings effectively requires either immersing them into a bath of molten zinc or applying zinc-rich paint which forms an organic bond with its surface and makes submersion unnecessary.
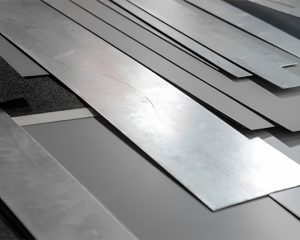
Beginning the process involves intensive cleansing and preparation of metal surfaces to rid them of impurities such as oil, rust, or scale, which will ensure proper adhesion between zinc and metal surfaces. Once these have been cleared away and dried off, immersing or spraying with paint rich with zinc may follow.
Submersion of metal into hot zinc causes a chemical reaction between zinc iron present within it and the metal itself, creating an alloy made up of both layers; this leaves behind an adherent corrosion-resistant surface coat of galvanized zinc whose thickness can be controlled by changing how long a piece remains submerged into its bath of zinc.
Zinc-rich paint can be applied to metal surfaces using various techniques such as brushing, spraying, or dipping. Once dry and cured, its composition forms a protective barrier against environmental corrosion that will last long into the future.
Galvanized coatings offer numerous advantages. First and foremost is their corrosion resistance, protecting the metal beneath from rusting and degrading. Furthermore, galvanized coatings have an extended lifespan–in some applications up to 50 years in some instances–along with being self-healing: should there be damage or scratches, zinc will form around its surrounding area to heal itself and cover over damaged spots on its own.
Galvanized coatings are widely utilized across a range of applications and industries. Common examples include roofing, steel fencing, and electricity transmission towers in construction as well as agricultural equipment, automotive components, and household appliances.
Galvanizing is an extremely durable and effective method to shield metals from rust. Through either hot-dip galvanizing or zinc-rich paint application, the galvanized coating provides a protective shield that extends its lifespan and increases the efficiency of metallic items in various industries.
Hot Dip Galvanized
Hot-dip galvanizing is an increasingly popular process used to apply protective zinc coatings to iron and steel surfaces, typically by immersing objects into a bath of hot zinc temperature ranging between 450 to 550 Celsius (850 degrees Fahrenheit). This results in a strong connection between steel and zinc which forms an anticorrosion coating that remains tough over time.
Hot-dip galvanizing begins by first thoroughly cleaning the metal to eliminate impurities such as oil, rust, or scale from its surface and ensure proper adhesion of zinc to steel. Next comes a dip into a bath of zinc where chemical reactions occur that produce galvanization.
Submersion in molten zinc causes it to react with iron present in steel, producing zinc-iron alloy layers and creating an adhesive surface coating on metals that adheres to them firmly; you can control its thickness by changing immersion times; typically thickness ranges from several micrometers up to 10 micrometers.
Hot-dip galvanizing offers outstanding protection from corrosion. The zinc coating acts as a physical barrier, blocking elements responsible for it from penetrating the steel substrate. If damaged or scratched, zinc corrosion occurs which protects surface areas under its protection, known as cathodic protective.
Hot-dip galvanized coatings have long-term durability. Their track record of protection for over fifty years in various applications makes galvanizing with hot dip an attractive solution for industries including construction, infrastructure, automobile agriculture, and many others.
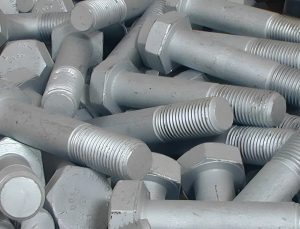
Hot-dip galvanized iron is widely utilized within the construction industry to construct structural components like beams, columns, pillars, fasteners, and fastener plates; architectural features like handrails guardrails, and gratings; transmission towers for electrical power transmission as well as highway safety barriers as well as agricultural machines are other uses for hot-dip galvanized iron.
Hot-dip galvanizing is an efficient and widely utilized process to protect iron and steel surfaces against corrosion, as its protective zinc coating forms an impregnating metallurgical bond with them, giving a long-lasting resistance against corrosion that’s ideal for many different industries.
Key Differences Between Galvanized and Hot Dip Galvanized
Although both hot dips galvanized coats involve applying an anticorrosive zinc layer onto steel objects.
There are some key distinctions between the two methods. Below are the main ones:
1. Thickness of Coating:
Galvanized: Galvanized surfaces generally consist of a thin zinc layer with a thickness ranging between several microns and 25 microns (0.001 inches).
Hot Dip Galvanized: Hot Dip Galvanized coating is generally thicker, usually between 50 to 150 millimeters (0.002 or 0.006 inches). Its thickness can be uniform or customized according to individual needs.
2. Adhesion between metal and substrate:
Galvanized: Galvanized coatings adhere mechanically to metal surfaces, adhering depending on surface roughness or irregularities for maximum adhesion. Adherence depends on adhering to both rough surfaces as well as irregular ones to ensure successful adhesion.
Hot Dip Galvanized: Hot Dip Galvanizing provides an effective metallurgical connection between zinc and metal surfaces, creating stronger and longer-term adhesion that is less susceptible to flaking, peeling, or flaking.
3. Corrosion Resistance:
Galvanized: Galvanized coatings provide exceptional corrosion protection under most circumstances; however, they may become susceptible to corrosion when exposed to extremely acidic or corrosive environments.
Hot Dip Galvanized: Hot Dip Galvanized Coatings provide superior corrosion resistance even in extremely corrosive marine environments. Their dense and uniform coating offers greater protection from corrosion, rust, and other forms of degradation.
4. Coverage and Uniformity:
Galvanized: Galvanized coatings may vary in coverage and thickness due to limited access or corners, meaning less coverage at edges or sharp angles due to limitations associated with this process.
Hot Dip Galvanized: Hot Dip Galvanized Coatings offer more uniform coverage and thickness and are suitable for covering complex shapes such as corners or edges with complex features. Immersion provides deeper penetration for greater coverage that yields consistent coating results.
5. Factors to Consider Regarding Cost:
Galvanized: Galvanizing is often more cost-effective than hot dip galvanization due to its thin coating and simple process, which make it more suitable for some situations.
Hot Dip Galvanized: Hot Dip Galvanization A more complicated and lengthy process than galvanizing can be more expensive initially; however, due to increased corrosion protection, it may justify this higher initial investment cost in certain cases.
Considerations must be given to these variations when selecting an optimal coating technique, taking into account project specifications, environmental considerations, desired durability, and budgetary constraints into account.
Comparison of Galvanized and Hot Dip Galvanized in Different Applications
Galvanized and hot dip galvanized coatings offer varying levels of protection and suitability for different applications.
Here’s a comparison of their use in various industries:
1. Construction Industry:
Galvanized: Galvanized coatings are widely employed in the construction industry for use on roofing fences, structural steel components, and HVAC systems, providing superior corrosion protection at a reasonable cost.
Hot Dip Galvanized Coatings: Hot dip galvanized coatings are highly sought after for applications that require significant force during construction work, such as bridges and highway safety rails, utility poles, and marine structures. Their stronger and longer-lasting protective layer resists corrosion better in harsh marine or highly corrosive environments.
2. Automotive Industry:
Galvanized: Galvanized Coatings can find application in automotive industries for smaller parts like brackets, fasteners, and other body pieces which offer moderate corrosion protection as well as cost efficiency. They offer moderate resistance against corrosion as well as cost efficiency.
Hot Dip Galvanized: Hot Dip Galvanization has become less prevalent within the automobile industry due to its more dense coating and potentially adverse effect on component tolerances, yet can still be useful in specific circumstances such as frame underbody components and chassis/exhaust systems that experience extreme conditions.
3. Electrical Industries:
Galvanized Coatings: Galvanized coatings are ideal for electrical applications where corrosion resistance is important, yet weight and thickness restrictions apply. Common applications for galvanized coatings are cable trays, conduits, and enclosures.
Hot Dip Galvanized: Hot Dip Galvanization may not be as popular among electrical contractors due to the weight and thickness of its coating; however, it can still be useful in grounding systems for electrical use or applications that demand long-term durability in harsh environments.
While some may see it as necessary others do not share that opinion and feel they need to change things up in order to remain competitive in today’s Marketplace.
4. Marine Industry:
Galvanized Coatings: These coatings may have limited applications in the maritime industry, particularly for smaller components or non-submerged applications. They offer moderate corrosion protection in aquatic environments but additional measures of protection may be necessary to provide complete resistance against corrosion.
Hot Dip Galvanized: Hot Dip Galvanized Coatings have long been utilized by marine sectors for shipbuilding structures offshore platforms shipbuilding, shipbuilding, and other applications that involve submerged exposure or submersion. Hot Dip Galvanized coatings have proven highly resistant to corrosion in saltwater as well as more acidic marine environments.
Always bear in mind that choosing between Galvanized and Hot Dip Galvanized coatings depends upon individual budget requirements as well as expected environmental conditions for any project. Hot dip galvanization provides superior protection in extreme environments but may be costly and have thickness restrictions; while galvanization offers cost-effective coverage in more moderate conditions.
Comparison Chart of Galvanized and Hot Dip Galvanized
Here’s a chart of comparison that highlights the main differences between Galvanized and Hot Dip Galvanized:
Aspect | Galvanized | Hot Dip Galvanized |
---|---|---|
Coating Thickness | Thinner (few microns to 25 microns) | Thicker (50 microns to 150 microns and more) |
Adherence to base Metal | Mechanical adhesion | Bonds made of metal |
Corrosion Resistance | Excellent in moderate environments | Superb, in the most corrosion-prone or marine environments. |
Coverage | Variations in coverage and thickness | A more uniform and complete coverage |
Suitability | Moderate environments, cost-effective | Heavy-duty applications, harsh marine environments |
Cost | Economic | Greater initial investment |
Conclusion
Galvanization is an indispensable process that protects metals from corrosion and extends their durability across various industries. Hot dip and galvanized coated coatings offer significant advantages; however, each can have significant differences that make them suitable for specific uses.
Galvanized coatings offer exceptional corrosion protection in moderate environments. Galvanization has many uses across automotive, construction, and electrical industries and has proven its resilience against rust. Galvanizing protects against rust while increasing longevity while decreasing maintenance costs.