Difference Between Sacrificial Anode and Impressed Current
A brief introduction to Sacrificial Anode and Impressed Current
Sacrificial anodes differ from impressed anodes by using an alloy or metal as the anode, rather than the one being protected. Conversely, impressed current use DC current to protect the metal to form its cathode instead.
Sacrificial and impressed current systems are two types of cathodic protection (CP). Furthermore, cathodic security can help safeguard metal surfaces against corrosion by providing an external cathodic flow to protect it.
Importance of understanding the difference between sacrificial anodes and the impressed current system
Understanding the difference between sacrificial anodes and impressed current systems is important for several reasons:
1. Effective Corrosion Protection: Selecting between sacrificial and enhanced current systems can significantly influence corrosion prevention efforts, with each offering distinct strengths and weaknesses in their ability to control corrosion. By understanding their differences, asset managers and engineers can select the one best suited to their particular needs while guaranteeing adequate corrosion protection for their structure.
2. Installation and Design of the System: Installation and design requirements vary significantly between sacrificial anodes and impressed current systems, so when selecting and placing them they require special consideration and replacement regularly. Conversely, impressed current systems necessitate more intricate considerations about power supply requirements as well as anode configurations – knowing these distinctions ensures it’s constructed and installed properly, increasing both its effectiveness and longevity.
3. Maintenance Considerations: Maintenance requirements and expenses vary for impressed and sacrificial systems. Sacrificial anodes require regular inspection and replacement while impressed systems need regular power supply maintenance checks as well as performance tests on anodes. Understanding maintenance needs helps develop appropriate maintenance plans and budgeting strategies for long-term cathodic protection system maintenance.
4. Applicability to Different Environments and Structures: Varying structures and environments may experience unique corrosion challenges; while certain environments might benefit more from using sacrificial anodes than current systems provide increased control and flexibility. Knowing the application of each system to various structures and environments provides more informed decisions during the planning and installation processes.
5. Conformance With Standards and Regulations: Various industry standards and regulations govern the selection and implementation of devices designed to ward off cathodic corrosion, such as anodes. By understanding how both traditional anodes and modern, redesigned systems differ, asset owners and engineers can ensure compliance with pertinent codes and rules, comply with necessary corrosion protection standards for their structures, and avoid operational or legal issues in doing so.
Understanding the difference between sacrificial and impressed modern systems is essential in selecting an effective corrosion protection solution, from installation and maintenance, through compliance with industry standards and regulations, all while increasing the durability, safety, and value of structures.
Sacrificial Anode
Sacrificial anodes are a type of cathodic protection mechanism used to halt or reduce corrosion on metallic structures. Made up of elements with increased chemical activity compared to what’s being protected, when connected electrically these anodes create galvanic coupling, protecting structures with increased reactive surface area from further corrosion.
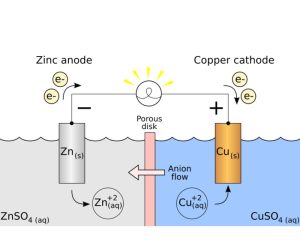
aluminum, zinc, and magnesium are commonly chosen as sacrificial anodes because these metals tend to corrode more readily when in contact with electrolytes such as water, soil, or concrete than structures they protect. Thus, these serve as effective protection for vulnerable structures but still corrode quickly over time if exposed.
In essence, they serve as an anode that corrodes easily while protecting critical infrastructure – thus serving as an anodic sacrifice material that corrodes away when they come in contact with electrolytes such as water, soil, or concrete while remaining secure against further corrosion damage.
Sacrificial anodes operate using galvanic corrosion as their foundation. As they corrode, electrons released by them travel through metal structures to form protective cathodic zones around them that alter their electrochemical potential into even greater positive (cathodic) states reducing corrosion.
Sacrificial anodes must be installed and chosen carefully to provide corrosion protection, taking into account factors like building type and size, environmental conditions, and electrolyte corrosivity when making this selection. Typically connected with electrical connections or bonding materials.
Over time, sacrificial anodes become depleted as they corrode, necessitating regular inspections and replacements to maintain optimal protection. Regular exams as well as replacements must occur for maximum efficiency of this system.
Sacrificial anode systems are frequently employed for corrosion protection on underground pipelines, ship platforms, offshore hulls, storage tanks, and reinforced concrete constructions. Installation and maintenance requirements are minimal while their lifespan is limited so regular replacement is required to provide desired corrosion protection levels.
Impressed Current
Impressed Current is a cathodic protection method that utilizes external power sources to supply precisely controlled direct current (DC). As opposed to using anodes as anode materials, current systems provide continuous electric current flow to stop corrosion.
When using impressed current, inert anodes are used instead of those which need to be sacrificed, constructed from materials like titanium or mixed metal oxide (MMO) coatings. These anodes are connected to power sources which include rectifiers for converting alternating voltage to direct current (AC to DC), with their position near structures needing protection being strategically chosen for security.
Once a power supply is turned on, it provides a controlled DC voltage to anodes. As part of this process, positive ions escape the surface of an anode into electrolyte solutions and form an anodic protective zone around structures while shifting their electrochemical potential toward less negatively charged conditions (cathodic). This cathodic zone acts to impede corrosion by protecting it from degradation by hindering its progress – thus protecting structures against further degradation.
Systems utilizing pressed current offer more control and flexibility than their counterpart, the sacrificial anode system. You can adjust the current output according to the specific needs of your structure as well as environmental corrosivity levels; control systems are frequently employed for optimal protection by monitoring its output and controlling it accordingly.
Pressed current systems can be utilized in large-scale projects such as offshore structures, bridges, storage tanks, and industrial installations. They offer extra corrosion protection in extremely acidic environments or for structures that need additional structural integrity protection.
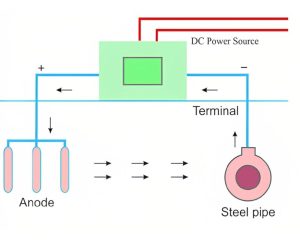
However, modern systems with impressed features require additional effort for construction, installation, maintenance, and testing compared to their sacrificial anode counterparts. They require a constant power source as well as regular monitoring of anodes’ performance as well as scheduled maintenance that ensures optimal operation; otherwise, inadequate care could reduce protection from corrosion and lead to structural damage.
Impressed current systems provide precise control and long-term corrosion protection, making them suitable for larger structures as well as challenging environments. Proper design, installation, and maintenance of impressed current systems are paramount to their efficient and effective operation.
Difference Between Sacrificial Anode and Impressed Current
The main difference between Sacrificial Anode and Impressed Current systems lies in their mechanisms of providing cathodic protection and their associated characteristics.
Here are the key differences:
1. Working Principle:
Sacrificial Anode: Sacrificial anodes function using galvanic corrosion principles. Anodes that consist of metals more active in corrosion become sacrificed more quickly to safeguard the structures they’re connected to.
Impressed Current: Impressed Current systems utilize an external source, like a rectifier, to provide controlled direct current (DC). This creates a protective cathodic zone around structures to avoid corrosion.
2. Anode Consumption:
Sacrificial Anodes: Sacrificial anodes are subject to gradual degradation due to corrosion. For optimal security levels, they should be regularly checked and replaced to ensure an efficient level of security.
Impressed Current: Impressed Current Systems don’t depend on anodes for corrosion protection; instead they use inert metal oxide anodes which won’t corrode significantly over time.
3. Controlling and Flexibility in Operations:
Sacrificial Anodes: Sacrificial anodes provide cathodic security primarily through passive means that require less adjustment, with their level of protection determined by their choice and placement.
Impressed Current: Compressed Current Systems provide greater control and flexibility to their system by offering adjustable power supplies to ensure cathodic security, with control systems used to regulate and monitor current flows.
4. Complexity and Size:
Sacrificial Anode Systems: Sacrificial anode systems tend to be easier to install and operation, which makes them ideal for powering smaller structures and applications.
Impressed Current: Impressed Current Systems that utilize current tend to be more complex when it comes to design, installation, and maintenance; typically used to build larger projects and structures which need additional levels of protection and control.
5. Maintenance Requirements:
Sacrificial Anode: Sacrificial anodes require regular inspection and replacement as they become consumed over time.
Impressed Current: System with Impressed Current Requires Regular Maintenance to Ensure Correct Operation* Impressed current systems require ongoing maintenance to ensure the correct functioning of anodes, power supplies, and any associated components.
Decisions between sacrificial anodes and current systems that are impressed can depend on several variables, including construction size, environmental conditions, budget constraints, and long-term maintenance strategies. Each approach offers advantages and disadvantages; making an educated choice will provide adequate corrosion protection.
Comparison Chart of Sacrificial Anode and Impressed Current
This chart compares the major difference between sacrificial and modern systems that are impressed:
Aspect | Sacrificial Anode | Impressed Current System |
---|---|---|
Working Principle | Galvanic corrosion | Direct current controlled (DC) |
Anode Consumption | Consumed over time | A very small or non-existent amount of anode is consumed. |
Control and Flexibility | Relatively passive | Greater control and greater adjustability |
Complexity of the System | Installation and operation is simple. | More complicated design and maintenance |
Maintenance Requirements | Periodic inspections and replacements | Monitoring and maintenance of the system regularly |
Applicability | Applications for smaller structures and structures | Larger structures and more challenging environments |
Cost Effectiveness | The cost-effective upfront investment, and the periodic replacement | Higher upfront cost, longer lifespan |
Environmental suitability | Different environments, including soils | Afflicting or challenging environments |
Regulatory Compliance | In compliance with industry standards and codes of conduct | Conformity to codes and standards of the industry |
Examples | Underground pipelines as well as boat hulls | Bridges, structures offshore |
Factors Influencing the Selection
When choosing between sacrificial anodes and current impressed systems to protect cathodics, many factors should be taken into consideration in order to select the optimal system for any purpose.
Here are the primary ones:
1. Materials and Type of Structure: The type and material composition of a structure plays an essential part in determining its system. Different materials offer differing levels of corrosion protection; some structures might even have specific needs; for instance sacrificial anodes may be appropriate for underground pipelines while current-based systems with impressed current may work better offshore or for large storage tanks.
2. Environmental Conditions: The environment plays a key role in determining which system to use; factors like soil composition, water salinity levels, temperature, pH levels and presence of pollutants will all impact this decision. Extremely corrosive environments might require additional controls or flexibility of current systems already implemented in place.
3. Project Budget and Cost Constraints: Budget for your cathodic system will be an essential element to take into consideration when choosing an anode protection cathodic system. Sacrificial anodes tend to be more cost-effective both initially and when installed; making them the go-to choice for projects with limited budgets. Decorative systems may cost more initially but over time may prove more economical due to their longevity and ability to control larger structures.
4. Plan for Long-Term Maintenance: It is important to carefully consider both the requirements for and Associated costs Associated with long-term maintenance. Anodes of sacrifice require regular examination and repair, which could incur maintenance expenses; modern systems pressed by pressure require surveillance, power supply maintenance, anode performance tests and surveillance maintenance plans as part of regular monitoring services; long-term maintenance plans should align with any system you select for optimal use.
5. Integrity to Existing Infrastructure Compatibility with Existing Infrastructure: When selecting a cathodic protection system, its capability should be carefully examined against your existing infrastructure systems and systems in place. You need to ascertain if your chosen system can easily fit in without disrupting or needing major adjustments or substantial modifications to be incorporated.
6. Compliance to Industry Standards/Regulations: Compliance to industry standards as well as codes and regulations is of utmost importance, especially since every industry and structure may have different corrosion protection needs. Choosing an anticorrosion system must meet applicable compliance standards in order to be used successfully.
Asset owners and engineers can utilize careful analysis of these elements to make informed decisions on the most suitable cathodic security system, be it sacrificial anodes or impressed current, to protect structures from corrosion while taking into account practical, financial, and long-term maintenance considerations.
Case Studies and Examples
Here are a few case studies and examples that illustrate the use of sacrificial anodes and impressed current systems in different applications:
1. Case Study on Sacrificial Anodes: Pipeline Protection Underground pipelines used to transport gas and oil typically use sacrificial magnesium anodes as corrosion protection. These anodes are placed regularly along the pipeline’s route and corroded intentionally to shield their contents from being affected by soil or water ingress.
2. Case Study: Offshore Structure Protection Offshore structures and platforms are exposed to harsh marine conditions that leave them susceptible to corrosion, making impressed current-based systems an effective means of protection. Offshore oil rigs might utilize cathodic impressed current protection using titanium or MMO anodes connected to rectifiers for cathodic protection current regulation – this allows precise control over cathodic current to ensure its durability as part of an overall corrosion strategy.
3. Example of Sacrificial Anodes: Boat Hull Protection The metal hulls of boats exposed to seawater can become susceptible to corrosion over time, so anodes composed of aluminum or zinc should be attached to their surfaces to provide corrosion-protection measures and ensure durability while also preventing destruction. Sacrificial anodes provide effective corrosion-deterrence solutions, with their long-term corrosion being diverted away from corroding parts of the vessel thus prolonging its durability and avoiding destruction.
4. Example of Impeded Current: Protection against corrosion of bridges located near coastal regions or exposed to salts used for deicing requires effective corrosion protection systems. Impressed current systems provide effective corrosion protection, with MMO-coated titanium anodes installed along their structures before connecting to rectifiers; this technology helps preserve bridge strength while prolonging their lifespan.
Case studies and demonstrations provide practical examples of using sacrificial anodes and inspired current systems across various industries to reduce corrosion and protect vital assets and infrastructure from degradation. They demonstrate how cathodic protection techniques are utilized to achieve this end.
Conclusion
Understanding the difference between sacrificial anodes and impressed current systems is essential to ensure effective cathodic protection. Sacrificial anodes rely on metal corrosion as a protection mechanism, while impressed current systems use external power sources to supply controlled current to avoid corrosion.
Decisions between sacrificial anodes and current impressed systems are driven by many variables, including design, environment conditions, project budget as well as long-term maintenance programs, integration into existing infrastructure and meeting regulatory requirements. Each option offers different advantages and disadvantages; so the optimal choice should reflect each specific application.