Intercalated and Exfoliated Nanocomposites
Intercalated and Exfoliated Nanocomposites are advanced materials characterized by different nanoparticle arrangements. Nanocomposites that are exfoliated or intercalated are very advanced substances in which nanoparticles can be dispersed in the matrix. It is typically the polymer. Nanocomposites are intercalated, particles are placed inside the matrix layer or stacked manner, and separated by a tiny space, which is known as gallery spacing.
The arrangement is created by introducing nanoparticles within the layers of the host material, usually via physical or chemical methods. Nanocomposites that are intercalated offer better properties including enhanced mechanical strength gas barrier properties and thermal stability.
Exfoliated Nanocomposites have been exfoliated, in contrast, they disperse nanoparticles in a uniform manner throughout the matrix without the absence of gallery space. They are achieved through techniques like mixing at high shear or solvent exfoliation. Exfoliated nanocomposites have exceptional properties, including higher mechanical strength, greater surface area, as well as improved electrical conductivity.
Definition of Intercalated Nanocomposites?
Intercalated nanocomposites are a subcategory of advanced materials in which nanoparticles are strategically integrated into a polymer matrix host material, usually by layering or stacking nanoparticles within their matrix host, creating what is known as gallery spacing between each layer.
Intercalated nanocomposites are distinguished from similar advanced materials by this particular arrangement of their nanoparticles in its matrix host, creating what resembles an ordered or stacked arrangement within it that contains tiny gaps between nanoparticle layers known as gallery spacing.
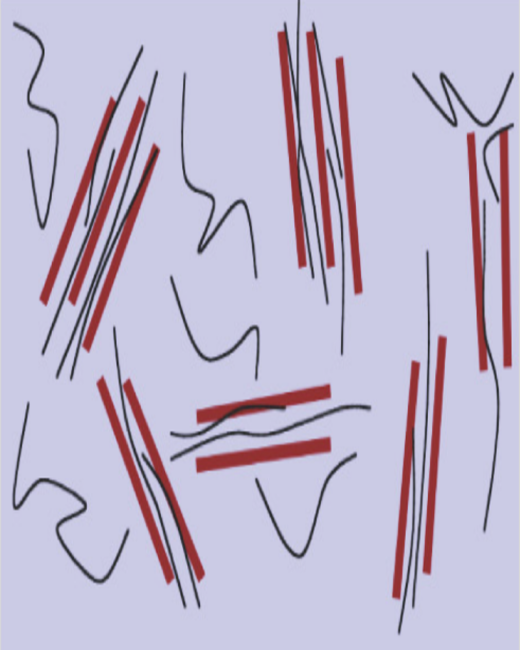
Intercalated nanocomposites are created by inserting nanoparticles such as clay minerals or nanoscale fillers between layers of host materials using techniques such as intercalation reactions, chemical bonding, or physical processes like melt mixing. This results in an intercalated nanocomposite with its own distinctive structure that confers several advantageous properties.
Intercalated nanocomposites feature enhanced mechanical properties, including increased stiffness and strength due to reinforcing agents within their matrix, Thanks to nanoparticle layers that act as reinforcing agents intercalated nanocomposites offer excellent barrier properties, making them suitable for applications that require resistance against gases or liquids, They have superior thermal stability due to an insulating effect from nanoparticle layers.
Automotive, packaging, and aerospace industries all rely on lightweight yet high-performance materials; intercalated nanocomposites offer such capabilities. Although achieving full dispersion can be challenging maintaining an intercalated structure can vary based on factors like nanoparticle choice and host matrix properties.
Intercalated nanocomposites remain an effective approach to creating customized materials to address specific industrial or technological requirements.
What are the different types of Intercalated Nanocomposites?
Here are some common types:
- Clay-Based Nanocomposites: Clay-based nanocomposites are the go-to choice when it comes to intercalated nanocomposites. Layered clays like montmorillonite and kaolinite serve as host materials while organic or inorganic nanoparticles are intercalated within their layers, often polyethylene or polystyrene matrixes are employed.
- Layered Double Hydroxide (LDH) Nanocomposites: LDHs consist of positively charged layers separated by anions and water molecules; in LDH nanocomposites, different anions, dyes or nanoparticles can be intercalated within these layers to create new materials with properties such as catalysis, drug delivery or flame retardancy applications.
- Metal Sulfide Nanocomposites: Nanoparticles composed of metal sulfides like MoS2 and WS2, when intercalated into layers can create nanocomposites with various applications ranging from lubricants and electronics to energy storage devices.
- Graphene-Based Nanocomposites: Graphene is a single layer of carbon atoms arranged in a two-dimensional structure that can be intercalated with various guest molecules or nanoparticles to form graphene-based nanocomposites, offering unique electronic, thermal, and mechanical properties used extensively in electronics, sensors, and advanced materials applications.
- Biopolymer Nanocomposites: Natural biopolymers such as cellulose and chitosan can be intercalated with nanoparticles for use as biodegradable materials, drug delivery vehicles, and tissue engineering applications.
- Polymer Nanocomposites: In this category, polymers serve as host matrices with various nanoparticles intercalated for improved mechanical, thermal, or barrier properties. They find wide usage across packaging, automotive, and aerospace industries.
- Silicate Nanocomposites: Inorganic silicates like zeolites and layered silicates can be intercalated with guest molecules or ions for use in catalysis, adsorption, and gas separation applications.
- Carbon Nanotube (CNT) Nanocomposites: CNTs can be intercalated into polymer matrixes or other materials to increase their electrical conductivity, mechanical strength, thermal properties, and overall functionality. Such nanocomposites have applications in electronics as well as structural materials.
- Metal Oxide Nanocomposites: Layered metal oxides such as niobates and titanates can be intercalated with different species such as organic molecules, ions or nanoparticles – providing applications in catalysis and electronics.
Definition of Exfoliated Nanocomposites?
Exfoliated nanocomposites are a class of advanced material where nanoparticles are evenly and precisely dispersed in the matrix of a host, typically made up of polymers. The word “exfoliated” refers to the method of segregating individual nanoparticles from their agglomerates.
While making sure they are evenly distributed throughout the matrix. The dispersion process is usually achieved via techniques like high-shear mix and solvent exfoliation.
One of the most important characteristics of exfoliated nanocomposites is that they do not have distinct galleries or layers that distinguish them in comparison to intercalated composites. Nanoparticles are distributed uniformly within the matrix leading to uniform microstructure.
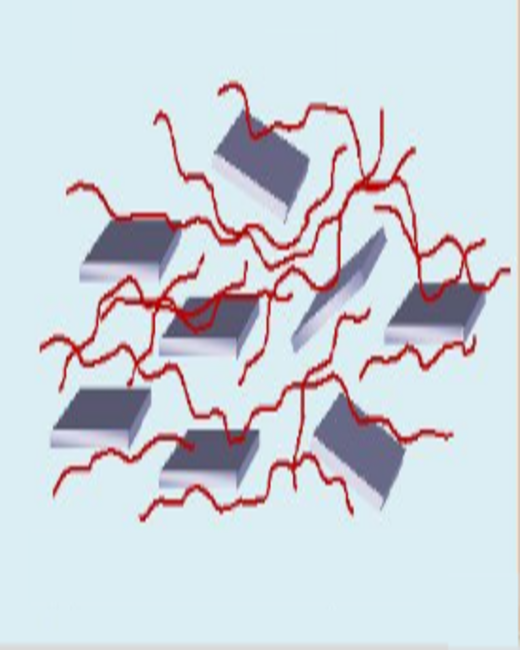
Exfoliated nanocomposites have numerous benefits, such as outstanding mechanical properties like increased tensile strength and toughness due to nanoparticles acting like strengthening agents. The larger size of the surface area of nanoparticles dispersed increases properties like heat conductivity, electrical conductivity, and gas barrier efficiency.
They are used in a wide range of areas, including electronic engineering, where enhanced electrical properties are crucial as well as in the creation of high-performance coatings. improved barrier properties are essential.
It is important to be aware that production methods for the exfoliated nanocomposites may be extremely energy-intensive, as well as maintaining a stable dispersion throughout the duration can prove to be difficult.
What are the different types of Exfoliated Nanocomposites?
Here are some common types:
- Graphene-Based Nanocomposites: Graphene is a 2-D carbon structure made up of one layer of carbon atoms that can be exfoliated and dispersed within various host materials such as polymers or metals, offering excellent electrical conductivity, mechanical strength, and thermal properties suited for applications in electronics, sensors, and advanced materials.
- Carbon Nanotube (CNT) Nanocomposites: CNT nanocomposites consist of single or multiwalled carbon nanotubes exfoliated and dispersed within polymers or other matrix materials for exfoliation, dispersion, and exfoliation for enhanced electrical conductivity, mechanical reinforcement properties and thermal properties that find use across aerospace, automotive and electronics industries.
- Layered Double Hydroxide (LDH) Nanocomposites: LDHs can be exfoliated into individual layers that are then dispersed throughout polymer matrix materials for nanocomposites with enhanced mechanical properties that can be utilized for flame retardancy, drug delivery, and coating applications. These nanocomposites demonstrate excellent flame retardancy properties.
- Nanoclay-Exfoliated Nanocomposites: Much like intercalated nanocomposites, nanoclays can also be exfoliated to form individual nanoplatelets which can then be dispersed throughout polymer matrix environments. Such nanocomposites offer improved barrier properties, mechanical strength, and thermal stability – qualities that make them particularly suitable for packaging and automotive materials.
- Transition Metal Dichalcogenide (TMD) Nanocomposites: Exfoliated TMDs such as molybdenum disulfide (MoS2) and tungsten disulfide (WS2) can be dispersed within polymers or other materials to form nanocomposites that have applications for lubricants, electronics, and energy storage devices.
- Nanoparticle-Polymer Nanocomposites: These composite materials consist of exfoliated nanoparticles such as metal oxides (e.g. titanium dioxide and zinc oxide), quantum dots, or magnetic nanoparticles that have been dispersed throughout a polymer matrix to form optoelectronic devices, catalysis catalysts or magnetic materials with applications spanning optoelectronics, catalysis and magnetic applications.
- Biopolymer Nanocomposites: Natural biopolymers like cellulose or chitosan can be combined with exfoliated nanoparticles for use as biodegradable materials, drug delivery systems, or tissue engineering applications.
- Exfoliated Silicate Nanocomposites: Layered silicates such as montmorillonite and hectorite can be exfoliated and dispersed into polymer matrixes to form nanocomposites used in films, coatings, and packaging materials.
- Exfoliated Metal Nanocomposites: Nanoparticles such as silver or gold nanoparticles can be dispersed in polymers for applications in electronics, catalysis, and antimicrobial materials.
- Bio-Nanocomposites: Exfoliated nanocomposites made of bio-based polymers such as starch or cellulose combined with nanoparticles provide eco-friendly materials and packaging solutions.
Difference Between Intercalated and Exfoliated Nanocomposites
Here’s a concise comparison chart highlighting the key differences between intercalated and exfoliated nanocomposites:
Feature | Intercalated Nanocomposites | Exfoliated Nanocomposites |
---|---|---|
Nanoparticle Arrangement | Layered or stacked | Uniform dispersion |
Gallery Spacing | Present (small gaps) | Absent |
Preparation Techniques | Intercalation methods | High-shear mixing, solvent exfoliation |
Mechanical Properties | Improved, but less than exfoliated | Exceptional |
Barrier Properties | Enhanced | High gas and liquid barrier |
Thermal Stability | Improved | Improved |
Electrical Conductivity | Typically lower | Enhanced |
Applications | Polymer nanocomposites, clay-based nanocomposites | Electronics, coatings, high-performance materials |
Challenges | Achieving complete dispersion, maintaining intercalation | Energy-intensive production, potential agglomeration |
What is the intercalation method of Intercalated and Exfoliated Nanocomposites?
Intercalation is one of the primary methods that is used to produce intercalated nanocomposites. It isn’t commonly used for the creation of nanocomposites that are exfoliated. The following is a description of the method used to intercalate the creation of intercalated nanocomposites.
Intercalated Nanocomposites:
Intercalated nanocomposites can be formed by intercalation. It involves the insertion of nanoparticles of clay minerals and other fillers at nanoscale, into the layers of host materials.
This process usually involves the next procedures:
- Selecting Nanoparticles: The most suitable nanoparticles include montmorillonite, a clay mineral that is layered and selected for the properties that are desired.
- Nanoparticle preparation: The nanoparticles are generally modified or treated in order in order to make them more compatible with host materials. They can be treated by using surfactants and other chemicals.
- Mixing with Host Matrix: The treated nanoparticles get blended with the host matrix of polymers, usually by melt mixing or processing. In this process, the nanoparticles get inserted into the layers of host material.
- Extrusion or casting: The nanocomposite mix is further processed typically through extrusion or casting, in order to make the end result.
Exfoliated Nanocomposites: Exfoliated nanocomposites do not rely on intercalation rather, they employ techniques such as high-shear mixing or solvent exfoliation to evenly disperse nanoparticles throughout their host matrix. Exfoliated nanocomposites do not possess distinct layers like intercalated ones and the nanoparticles are evenly dispersed across its entirety, producing different properties and applications for exfoliated compositions.
How do Intercalated and Exfoliated Nanocomposites Differ in Properties?
Mechanical Properties:
- Intercalated Nanocomposites: Intercalated nanocomposites show enhanced mechanical properties in comparison to the host material in its pure form which include increased stiffness and toughness. But, the improvement tends to be less noticeable than that of exfoliated nanocomposites.
- Exfoliated Nanocomposites: The nanocomposites exfoliated have exceptional mechanical properties. They typically show an impressive increase in the strength of tensile, hardness, and modulus as a result of the uniform distribution of nanoparticles, which act as reinforcement agents.
Barrier Properties:
- Intercalated Nanocomposites: Intercalated nanocomposites offer enhanced barriers to liquid and gas in comparison to the natural host material. Gallery spacing between nanoparticles could hinder the penetration of molecules.
- Exfoliated Nanocomposites: Nanocomposites that have been exfoliated typically show excellent gas and liquid barrier properties due to evenly dispersed nanoparticles that provide a tortuous pathway for the diffusion of molecules.
Thermal Stability:
- Intercalated Nanocomposites: Intercalated nanocomposites usually exhibit better thermal stability as relative to the host material. Nanoparticles can serve as barriers to insulation, thereby reducing heating transfer.
- Exfoliated Nanocomposites: The exfoliated nanocomposites have improved thermal stability. However, their uniform dispersion could provide more uniform and dependable thermal resistance.
Electrical Conductivity:
- Intercalated Nanocomposites: Intercalated nanocomposites might exhibit limited improvements in electrical conductivity when compared with the host material in its pure form due to the fact that the structure of the layers could limit the mobility of electrons.
- Exfoliated Nanocomposites: The nanocomposites with exfoliation typically have an increase in electrical conductivity thanks to the nanoparticles that are dispersed well, which facilitates better electron transportation.
Benefits and Applications of Intercalated and Exfoliated Nanocomposites
Intercalated Nanocomposites:
- Mechanical Properties of Intercalated Nanocomposites: Intercalated nanocomposites possess improved mechanical properties, such as increased tensile strength and stiffness, making them desirable in industries like automotive, aerospace, and construction for lightweight yet high-strength components.
- Enhance Barrier Properties: Intercalated nanocomposites featuring gallery spacing have superior barrier properties to other nanomaterials and thus are suitable for packaging materials aimed at stopping oxygen and moisture permeation, where keeping these permeations to an absolute minimum is key.
- Thermal Stability: Intercalated nanocomposites offer improved thermal stability due to the insulating effect of nanoparticle layers. As such, they’re often utilized in applications requiring resistance against high temperatures, for instance, flame-retardant applications.
- Reduced Material Consumption: Strengthening host materials allows intercalated nanocomposites to reduce material usage, leading to cost savings and environmental perks.
- Applications: Intercalated nanocomposites have multiple uses including polymer nanocomposites, clay-based materials, and corrosion protection coatings.
Exfoliated Nanocomposites:
- Extraordinary Mechanical Properties: Nanocomposites that have been exfoliated have exceptional mechanical properties including high tensile strengths along with toughness, modulus, and strength that make them ideal to be used as structural elements for automotive, aerospace, as well as sports equipment.
- High Surface Area: The huge size of the surface area that nanoparticles are dispersed on exfoliated nanocomposites improves their properties such as electrical conductivity and catalytic activities, which allows the use of electronics, sensors, and catalysis.
- Excellent Barrier properties: Nanocomposites that have been exfoliated provide superior liquid and gas barriers because of the uniform dispersion and distribution of nanoparticles. They are ideal for use in packaging and coatings.
- Increased Electrical Conductivity: Nanocomposites can be found in various conductive material, which includes the conductive polymers and composites vital to electronic devices and parts.
- The Nanostructured Material: Exfoliated Nanocomposites aid in the creation of novel nanomaterials and nanocomposites that possess unique properties as well as applications in nanotechnology.
- Storage and Conversion of Energy: Storage and Conversion can be found for energy storage systems, such as supercapacitors and batteries, and also for energy conversion technology like photovoltaics, fuel cells, and so on.
Summary
Intercalated and Exfoliated nanocomposites are advanced materials characterized by different nanoparticle arrangements. Intercalated materials feature particles sandwiched between layers, creating “gallery spacing.” Intercalated nanocomposites are created using intercalation techniques and possess moderate mechanical and barrier properties.
Exfoliated nanocomposites disperse nanoparticles throughout a matrix without distinct layers separating their dispersion. Exfoliated nanocomposites are produced through high-shear mixing or solvent exfoliation processes that produce exceptional mechanical properties, high surface area, and improved electrical conductivity.
Reference
Here’s a list of reference books on the topic of nanocomposites and related subjects that can be valuable for research and further exploration:
- “Nanocomposites: Materials, Manufacturing and Engineering”
- “Polymer Nanocomposites: Processing, Characterization, and Applications”
- “Nanomaterials: Synthesis, Properties and Applications”
- “Nanocomposites: in Electrochemical Sensors”
- “Nanocomposites: Ionic Conducting Materials and Structural Spectroscopies”
- “Nanocomposites: Vol. 2 of Frontiers in Materials”
- “Exfoliated and Laminated Nanocomposites“
- “Nanocomposite Science and Technology“
- “Polymer Nanocomposites: Advances in Filler Surface Modification Techniques”
- “Handbook of Nanomaterials for Industrial Applications”