A brief introduction to Inconel and Monel
Inconel and Monel differ principally by being composed of nickel-chromium alloys; on the other hand, Monel contains nickel and copper as its constituent elements. Inconel and Monel have become staples in industrial settings, thanks to their extreme corrosion-resistance alloy compositions. While both types may seem expensive to produce, their production costs remain prohibitive.
Importance of understanding the differences between Inconel and Monel alloys
Understanding the difference between Inconel and Monel is vitally important, for several reasons:
1. Material Selection: Each alloy offers distinctive properties that make it suitable for certain projects, making engineering and manufacturer select the ideal alloy based on requirements like corrosion resistance, strength, and temperature stability. An informed material choice can ensure optimal performance and durability of components or structures.
2. Corrosion Resistance: Inconel and Monel both exhibit different degrees of corrosion resistance depending on their environment. Inconel exhibits exceptional resistance against high temperatures, oxidation, and sulfidation corrosion while Monel stands up well to marine, and chemical corrosion as well as hydrofluoric acids and alkaline solutions.
Having this knowledge allows you to select an alloy appropriate for the most hostile of corrosive environments.
3. Mechanical Properties: Inconel alloys and Monel alloys possess distinct mechanical properties such as strength and toughness, making them well suited to applications involving heat or thermal stress.
Inconel can retain its mechanical properties even at elevated temperatures, while Monel is tough and strong at various temperatures including cryogenics – understanding these differences helps you select an alloy suitable for the task at hand.
4. Application Suitability: Due to their diverse properties, Inconel or Monel metal alloys are utilized in different industries. Inconel can be found in applications like aerospace, gas turbines, power generation and chemical processing while Monel tends to be preferred in marine applications, offshore equipment use and chemical/petrochemical processing.
Understanding which applications each metal alloy serves will ensure it can be optimally utilized and will maximize performance.
5. Fabrication and Machinability: Inconel and Monel have different properties when it comes to fabrication, welding, heat treatment and machining; understanding these differences is vital in handling materials used for manufacturing, assembly and maintenance processes.
Knowing fabrication requirements will help avoid potential issues while guaranteeing integrity and quality in final product delivery.
6. Cost and Availability: Inconel and Monel vary significantly when it comes to price and availability. Inconel alloys tend to be more costly, with limited sizes and shapes. By contrast, Monel is generally more affordable and widely available – this information is important in understanding budgetary concerns as well as feasibility of using alloys for specific projects.
Understanding the distinctions between Inconel and Monel allows for informed decisions on material selection, design, fabrication and application of both alloys. When selecting an Inconel alloy for use on any given project, its performance, durability and cost effectiveness must meet project requirements in terms of performance, durability and cost efficiency.
What Is Inconel?
Inconel is the trade name for a grouping of superalloys made from austenitic Nickel and Chromium alloys, specially optimized by manufacturers to meet even the most demanding environments. Inconel boasts exceptional thermal resistance; maintaining its tensile strengths at extreme heat.
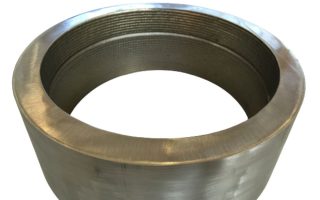
Costly alloys have the capacity to withstand extreme heat while remaining corrosion and oxidation-resistant, creating a thick and stable oxide layer when heated that protects their surfaces from further heat attack.
Inconel is often preferred over stainless steel in heat treatment applications involving rapid temperature changes, exposure to seawater or jet engines, and jet engines in terms of rapid temperature shifts or exposure, rapid temperature change exposure, or jet engines. Inconel can also be found used as gas turbine blade material and fasteners at higher temperatures for fasteners at high temperatures as well as seals.
What Is Monel?
Monel is the brand name for a family of nickel-copper alloys with typically 52-67% nickel content. These alloys also contain copper, iron, manganese, and carbon; so called because their composition primarily comprises these substances.
Monel alloy is stronger than pure Nickel and resistant to corrosion caused by various agents like seawater, as well as fabrication methods like hot and cold working, welding, and machining. Fabrication methods may include hot-and-cold working, welding, and machining – fabrication methods that make this alloy quite expensive – Monel piping costs three times more than carbon steel! However, its use remains limited.
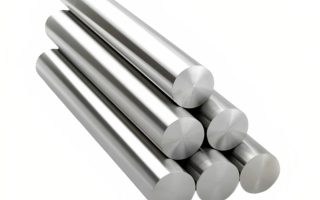
Monel 400 and Monel 401 alloys can be found widely across numerous fields, such as aerospace, oil production and refining, musical instruments, and marine applications – not to mention many more applications besides these three areas. There are multiple grades of Monel available as well, including 404 which is most frequently seen used today.
Difference Between Inconel and Monel
Composition and Alloying Elements
Inconel:
Inconel alloys feature nickel as their primary alloying element, contributing significantly to their composition and providing them with excellent corrosion resistance as well as high-temperature strength. This provides them with both excellent corrosion protection and strength at higher temperatures.
Inconel alloys also contain various amounts of chromium, which contributes to their increased resistance against oxidation and sulfuration as well as corrosion due to their presence. Thanks to chromium’s presence, Inconel alloys also possess excellent corrosion resistance.
Inconel alloy compositions also contain molybdenum and iron in small amounts, along with cobalt and titanium, all of which contribute to improving mechanical properties such as toughness, strength, and resistance to fatigue and deformation.
Monel:
Nickel and copper alloys form the basis of Monel alloys, with copper providing numerous beneficial properties such as improved corrosion resistance in marine environments and an increase in chemical corrosion resistance, making Monel an excellent choice for use in environments containing aggressive chemicals.
Monel alloys may include components other than nickel and copper, including iron, manganese, and even small amounts of carbon-silicon and sulfur which may help improve production or modify certain properties of the alloy. These trace elements can help increase its efficiency or change certain properties of Monel.
Inconel alloys consist primarily of nickel, with other elements added such as chromium to improve corrosion resistance and mechanical characteristics. Monel alloys feature both elements; copper is key in improving its corrosion resistance properties.
Corrosion Resistance
The corrosion resistance of materials is an essential consideration when selecting them for any application, and both Inconel and Monel offer excellent corrosion protection; their performance varies depending on their environment of use.
Inconel:
Inconel alloys are widely renowned for their resistance to corrosion in high-temperature environments with aggressive conditions, particularly at higher temperatures and more aggressive solutions such as acids, alkalis, or salt solutions.
Inconel’s corrosion resistance remains consistent even at higher temperatures making these alloys suitable for applications involving heat stress such as aerospace, nuclear reactors, power generation, or chemical processing where harsh environments must be met with no resistance from corrosion or erosion.
Monel:
Alloys made of monel offer excellent corrosion resistance in both marine and chemical environments, including seawater environments. Seawater-resistant monel alloys make ideal marine applications like seawater pumps, propeller shafts, and valves.
In addition, monel alloys can withstand an assortment of chemicals such as acids, alkalis, and reducing agents; additionally, they offer resistance against hydrofluoric acids which makes them suitable for industries like chemical processing and petrochemicals.
Inconel and Monel are both corrosion-resistant materials; however, their performance varies based on the environment they will be used in. Monel performs better at high temperatures whereas Inconel excels in chemical and marine corrosion applications. When selecting either material it’s essential to consider both your application needs as well as where you plan to use them.
Strength and Mechanical Properties
Strength and mechanical properties play a critical role when selecting materials for various applications. While Inconel and Monel vary slightly in terms of mechanical strength and resistance to corrosion respectively, both alloys offer outstanding mechanical and strength properties.
Inconel:
Inconel alloys are widely renowned for their strength at elevated temperatures, in particular their resistance to deformation and heavy loads. Their tensile resistance enables them to withstand deformation while being tough enough to withstand impact and fracture, maintaining mechanical properties even under extreme temperatures and thermal cycling conditions.
Furthermore, Inconel alloys possess excellent fatigue resistance which makes them suitable for applications where repeated stress or load cycling takes place such as aerospace, gas turbines, and power generation industries where temperature stability and strength stability are crucial.
There is one final option worth noting when considering whether to open an escrow account: contacting a broker directly who specializes in foreign trade to facilitate a sale and ensure a quick closing transaction process for you. This strategy has proven highly successful at increasing investment returns over time – for both sellers and purchasers of such properties.
Monel:
Monel alloys feature excellent mechanical properties and resistance to wide temperature ranges, such as being corrosion resistant.
Their high tensile resistance ensures structural integrity and resistance against deformation; additionally, they have excellent shock-absorbency as well as being easy to form into desired shapes – ideal for low-temperature applications such as marine applications, oil & gas equipment or chemical processes where corrosion resistance and strength are of key importance. Monel alloys are widely used across these fields.
Inconel and Monel both possess excellent mechanical and strength properties; however, when selecting either material it is essential to take into account each application’s individual requirements. Inconel may be preferred when working in high-temperature applications with thermal stresses, fatigue resistance or where high levels of toughness or toughness are desired across a broad temperature range including cryogenics;
Monel can offer strength, toughness, and ductility with flexible temperature range applications requiring strength toughness or ductility requiring strength/toughness/ductility requirements across a broad temperature spectrum including cryogenic applications. To make an informed choice it is imperative to fully understand each application’s mechanical needs before selecting either Inconel or Monel material.
Applications
Inconel and Monel alloys find applications across industries and sectors due to their unique properties and capabilities.
Here are some key applications of each alloy:
Inconel:
1. Aerospace Industry: Inconel alloys have long been recognized for their exceptional high-temperature strength, corrosion resistance and oxidation resistance in the aerospace industry, making it popularly used for components like turbine blades, combustors and exhaust systems on jet engines.
2. Gas Turbines and Power Generation: Inconel alloys have found use in gas turbines and power generation Equipment, such as turbine blades, combustion chambers and heat exchangers, due to their superior strength at high temperatures as well as corrosion resistance properties. They’re an ideal material choice for these demanding applications due to their excellent resistance.
3. Chemical Processing Plants: Inconel alloys have proven themselves adept at withstanding harsh environments and high temperatures of corrosion oxidation, making them suitable for use in reactors, heat exchangers and vessels that handle potentially toxic substances.
4. Nuclear Reactors: Inconel alloys are widely utilized in nuclear reactors due to their resistance to corrosion, high temperature stability and radiation protection properties. These alloys can be found in reactor cores, steam generators and other essential components.
Monel:
1. Marine Applications: Monel alloys have excellent corrosion-resistance in marine environments and are frequently utilized in seawater equipment like valves, pumps, propeller shafts and heat exchangers.
2. Offshore Equipment: Monel alloys are highly suitable for offshore uses in the oil and gas industry, including oil platforms, subsea pipelines, and offshore drilling equipment that is exposed to seawater.
3. Chemical and Petrochemical Processing: Monel alloys are widely employed in the chemical and petrochemical industries due to their resistance to harsh chemicals. Reactors, distillation columns, valves and pipes all benefit from using monel.
4. Electrical and Electronic Components: Monel alloys can be found in many electrical and electronic components that require corrosion resistance and conductivity, including connectors, switches, springs, and electrical contacts.
Note that these applications of Inconel and Monel alloys are by no means exhaustive; both materials may find use in other industries or niche applications due to their unique properties. Selecting an alloy depends on factors like corrosion resistance, strength, temperature stability and other variables relevant to each particular use case.
Fabrication and Machinability
Due to their special properties and characteristics, Inconel and Monel alloys require special care when fabricating or machining them.
Their difficult working characteristics and individual traits make these alloys particularly challenging to work with:
Inconel:
1. Machinability: Inconel alloys are notoriously difficult to machine when compared with other alloys due to their high strength and work hardening characteristics, leading to rapid tool wear rates, as well as difficulty in creating smooth surfaces. Specialized techniques for Inconel alloy machining as well as coolant systems must be implemented when processing this metal alloy.
2. Welding: Inconel alloys can be welded using several techniques, including gas tungsten-arc welding, gas metal-arc welding, and shielded metal-arc welding. However, due to Inconel’s high melting point and tendency towards cracking and heat-affected zones (HAZs), welding presents its own set of challenges; preheating before welding as well as heat treatment post welding may be required in order to minimize cracking; for optimum results precise control over welding parameters is often needed in order to minimize cracking.
3. Forging and Extrusion: Inconel alloys can be easily formed using cold and hot work, extrusion, forging, and other processes. However, due to their high strength, they require careful handling when being formed using appropriate tools, lubrication, and annealing. After fabrication heat treatment may also be required in order to improve or restore the properties of the alloy.
Monel:
1. Machinability: Monel alloys tend to be easier than Inconel for machining purposes. These alloys tend to be more ductile and less brittle, making machining simpler overall. However, work hardening poses challenges that necessitate using appropriate cutting speeds, feed rates, and tool materials for optimal machining results.
2. Welding: Monel alloys can be welded using similar techniques to Inconel, such as GTAW, GMAW, and SMAW welding processes. As with Inconel alloys, Monel can crack during welding as well as produce HAZ issues; to minimize these concerns it is often necessary to employ preheating techniques, regulate interpass temperature settings and perform post-weld treatments in order to meet all safety criteria.
3. Forming and Fabrication: Monel alloys can be easily formed using cold working, bending, and rolling methods. In general, Monel is more ductile than Inconel; as with any material it is important to consider proper tooling, lubrication, and any spring back stresses during forming operations.
Fabrication and machining of both Inconel and Monel require special considerations and techniques due to their respective high strength levels. Inconel alloys tend to be more difficult to work with while Monel alloys offer greater machinability. Heat treatment may be required in order to achieve desired results with both alloys.
Cost and Availability
When selecting materials, it is essential to take cost and availability into account.
Here is information regarding Inconel, Monel, and other alloys’ availability and costs:
Inconel:
1. Cost: Due to the combination of their high nickel content and other alloying components, Inconel alloys tend to be relatively more costly compared to other metal alloys. Nickel itself is an expensive material; adding other alloying elements only increases costs further. Inconel prices depend on which form and grade you purchase;
2. Availability: The availability and form of Inconel alloys depend upon their intended use. While some grades, such as Inconel 600 or 625, may be widely available, more specialized or specialty alloys as well as sizes with longer lead times may have limited supply.
Monel:
1. Cost: Monel alloys are typically more cost-effective compared to Inconel alloys. While they still contain nickel, the addition of copper in Monel alloys helps to lower the overall cost. The specific grade and form of the Monel alloy can influence its price.
2. Availability: Monel can typically be more easily found than certain grades of Inconel, such as Monel 400. Availability may depend upon grade and size requirements; please inquire further if needed.
Important to keep in mind is the fluctuation of price and availability for Inconel and Monel alloys depending on market conditions, demand/supply dynamics, supplier location, distributor availability, etc. To get accurate information regarding pricing and availability for specific alloys of Inconel/Monel it’s a good idea to speak directly with distributors or material suppliers.
While cost should always be taken into Consideration when making this choice, selecting an alloy that best meets both technical specifications and performance expectations should also be a top priority.
Comparison Chart of Inconel and Monel
Here is a chart that highlights the main differences between Inconel and Monel:
Aspect | Inconel | Monel |
---|---|---|
Composition | Nickel, chromium and other metals | Nickel, copper and iron |
Corrosion resistance | Resistance to oxidation, sulfation and high temperatures | Resistant to alkaline and hydrofluoric solutions, and marine environments. |
Strength and Mechanical Properties | Excellent fatigue resistance, high strength and exceptional properties at elevated temperature | Excellent strength and properties at all temperatures. Suitable for cryogenic conditions |
Apps | Chemical processing, nuclear reactors, aerospace, gas turbines | Chemical and petrochemical processes, electronic components, marine applications, offshore equipment |
Fabrication and Machinability | Welding challenges, poor machinability and specialized machining required | Welding considerations, better machinability and softer, more ductile materials |
Cost and Availability | Availability may vary by grade and size. | More widely available, more cost-effective |
Similarities Between Inconel and Monel
Inconel and Monel share many similarities despite having unique properties and characteristics.
Here are some notable parallels:
1. Nickel Content: Both Inconel alloys and Monel contain significant quantities of nickel, which plays a crucial role in their corrosion resistance properties. However, the exact proportions and ratios vary.
2. Corrosion Resistance: Inconel alloys and Monel are widely known for their superior corrosion resistance properties in chemical and marine environments, respectively.
3. Industrial Applications: Inconel and Monel alloys find use across several industrial sectors. Their corrosion-resistant, strength, and other desirable qualities make these alloys popular choices in aerospace, chemical processing, oil & gas sectors as well as others.
4. Combination alloys: Both Inconel (Monel) and Monel (Inconel) alloys may contain small amounts of additional elements to further improve certain properties; the exact composition will depend on both alloy grade and application requirements.
While both alloys share some similarities, their differences are much greater, particularly in terms of composition, corrosion resistance and strength. Their differences allow each alloy to better suit different environments and applications.
Conclusion
Inconel and Monel are two distinct alloys with their own set of properties that set them apart. While both alloys offer corrosion protection for multiple industries, their composition, corrosion resistance strength, mechanical properties fabrication cost, and availability differ considerably between the two alloys.
Alloys made of nickel are known for being resistant to corrosion and oxidation at high temperatures, offering strength, mechanical properties, and fatigue resistance in an aggressive environment. Inconel alloys have applications across industries like aerospace, gas turbines, and power generation.