Bainite and Martensite
Bainite and Martensite are two distinct microstructures found in steel alloys during phase transformations, where diffusion-controlled processes yield mixed phases such as ferrite and cementite that exhibit an acicular morphology for increased toughness perfect for automotive components and machinery components which need a balance between strength and ductility.
martensite forms at lower temperatures through diffusionless transformation and results in an extremely strained, tetragonal crystal structure with exceptional hardness and strength, yet its highly stressed state renders it fragile. Its hardness often makes martensite an appealing material choice for cutlery blades and springs proper tempering is often necessary to reduce.
Its brittleness bainite and martensite both demonstrate how complex relationships exist among microstructure, properties, and processing conditions in materials science.
what is Bainite?
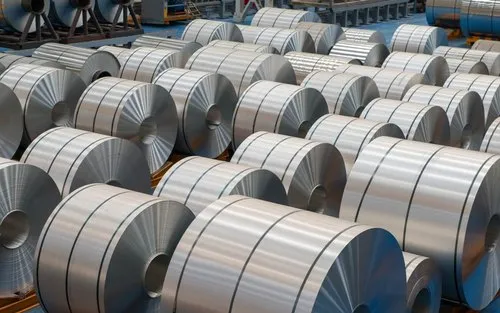
Bainite is a distinct microstructure found in steel and other alloys during phase transformations, named for British metallurgist Edgar C. Bain who first identified its characteristics. Bainite forms at intermediate temperatures between those required for austenite to become ferrites or pearlites and those necessary to form bainite from austenite transformation into ferrites or pearlites creating gradual structural transformation instead of its rapid counterpart martensite formation.
Bainite microstructure comprises both ferrite and cementite phases, with the former having needle-like or acicular structures that give bainite its distinctive appearance. There are two forms of bainite; upper bainite forms at higher temperatures while exhibiting coarse needle structures while the latter occurs at slightly lower temperatures exhibiting finer acicular structures.
One of the main advantages of bainite over pearlite lies in its improved mechanical properties. While offering relatively higher strength and hardness than pearlite, bainite also maintains levels of ductility and toughness not seen in martensite properties which make bainite suitable for applicationa.
Including automotive components, structural parts, and machinery as well as being transformed via isothermal transformation and tempering processes for further optimizing its mechanical characteristics.
Bainite represents an integral component in materials science, illustrating its complex interrelations of phase transformations, crystal structures, and material properties that result.
what is Martensite?
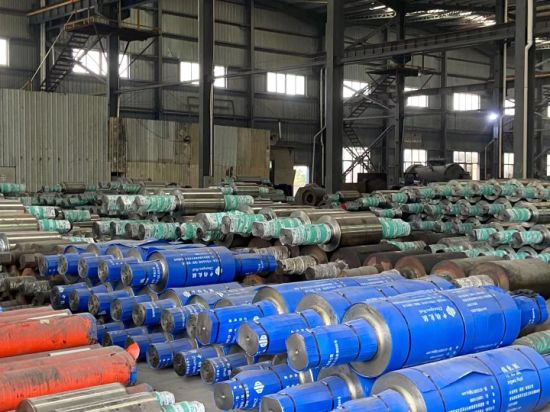
Martensite is an unusual microstructure found in steel and other alloys as a result of diffusionless transformation, usually following rapid cooling from an austenitic phase at high temperatures. Named for German metallurgist Adolf Martens, its needle-like or lath-shaped appearance results from crystal lattice distortion caused by this transformation process.
Transformation to martensite involves an almost diffusion-less rearrangement of atoms that leads to an intense strain in its crystal structure, producing a tetragonal shape characterized by remarkable hardness and strength; making martensite an appealing material choice for applications requiring wear resistance as well as high strength properties.
Its inherent fragility should be mitigated as part of any solution for better wear resistance or increased strength properties. Its inherent fragility requires constant care during its fabrication to minimize risks to users and workers.
Martensite can be altered through tempering to increase its ductility and toughness, thus improving both its hardness and toughness under load. This involves heating it back to a specific temperature range before subjecting some martensite crystals to undergo transformation into more stable forms known as “tempered martensite”, thus providing optimal hardness balanced by increased toughness as well as reduced susceptibility to cracking under load.
Martensite plays an essential part in various applications, from blade production and tool making to spring manufacturing where its hardness plays an instrumental role. Its formation and subsequent tempering highlight the profound influences of cooling rates, alloy composition, and heat treatment processes on microstructure development and mechanical properties of materials.
The Role of Alloying Elements in Bainite and Martensite Formation
Alloying elements play an instrumental role in shaping steel’s and other alloy’s microstructures, including bainite and martensite formation, to produce unique microstructures such as bainite or martensite microstructures that determine phase transformation kinetics, crystal structure formation, and material properties.
Silicon, manganese and chromium alloying elements have an influence on the transformation kinetics during bainite formation by altering diffusion rates within its material. Silicon can slow carbon diffusion rates within it which affects its growth into bainitic ferrite formation.
While manganese and chromium can speed its nucleation by providing extra resources needed to form new phases and promote bainite nucleation processes. These alloying elements also alter its morphology by changing the size or shaping of its acicular ferrite structures significantly
Martensite formation depends upon alloying elements like carbon and certain austenite stabilizers such as nickel or manganese to set its starting temperature (Ms) and hardness. Higher carbon contents tend to reduce this threshold temperature, making its formation possible at lower quench temperatures than anticipated during quenching. Austenite stabilizers, on the other hand, may delay transformation to martensite thus altering both its kinetics and microstructure significantly.
Alloying elements play an integral part in shaping both bainite and martensite formations; specific alloy additions to bainite may enhance its strength-toughness balance while in martensite they influence hardness, strength levels, and susceptibility to embrittlement – thus being essential to achieve desired microstructures and mechanical characteristics in bainite or martensite formations.
The selection of alloying elements during materials design and processing processes must take this factor into consideration in order to reach desired microstructures and mechanical characteristics in bainite and martensite formations.
The Crystal Structure of Bainite and Martensite
Barite and martensite possess distinct crystal structures which play an integral part in their properties and behavior.
Bainite: The crystal structure of bainite primarily comprises two phases; these being ferrite and cementite. Ferrite has a body-centered cubic (BCC) crystal structure consisting of iron atoms in its corners and center that allow diffusion of carbon into its lattice matrix. On the other hand, Cementite boasts an orthorhombic crystal structure composed of alternate iron and carbon atoms in an orthorhombic lattice network structure.
bainite’s needle-like structure results from diffusion-controlled transformation processes. Ferrite plates or needles are separated by thin layers of cementite to give bainite its distinctive appearance while its improved toughness surpasses other microstructures, like martensite.
Martensite: Martensite is formed through a diffusionless transformation from austenite. Austenite contains face-centered cubic (FCC) crystal structures; during rapid cooling that leads to martensite formation, their FCC lattice distorts into tetragonal form due to strain and stress introduced into its lattice by rapid cooling processes resulting in characteristic needlelike or lath-shaped structures seen with martensite crystal structures.
Martensite achieves its remarkable hardness and strength due to a distortion in its lattice structure and specific arrangement of atoms within it, driven by energy minimization associated with lattice distortion. Transformation takes place almost instantly during cooling.
How Bainite and Martensite Form in Steel
Bainite and martensite are microstructures found within steel formed through different phase transformation processes, producing unique crystal structures with unique mechanical properties.
Bainite Formation in Steel: Banite can form in steel when austenite (the high-temperature phase with a face-centered cubic crystal structure) transforms at intermediate temperatures into an assortment of ferrite and cementite (iron carbide) phases through a diffusion-controlled process, rather than rapid quenching such as required for martensite formation.
bainite formation involves both nucleation and growth processes. At first, small regions of ferrite and cementite begin nucleating within austenite grain boundaries before growing out to form needle-shaped structures called needle-brite nuclei as the transformation continues. These unique needle structures result from diffusion-controlled growth processes which enable gradual transitioning as opposed to martensite’s abrupt changes during formation.
Martensite Formation: Martensite is formed when austenite is rapidly cooled or quenched at room temperature and quickly quenched subsequently, unlike bainite which requires diffusion to change to martensite atoms can rearrange themselves into their new crystal structure without lengthy diffusion across long distances.
Quenching transforms face-centered cubic (FCC) austenite lattices to body-centered tetragonal (BCT) crystal structures of martensite through rapid cooling; rapid cooling prevents carbon atoms from diffusing to their preferred positions within this new crystal lattice, producing distortion and high internal stress that characterize martensite; this lattice distortion gives martensite its high hardness and strength as well as making it relatively brittle.
bainite and martensite formation rely heavily on alloying elements – particularly carbon – as well as cooling rate to be successful. Carbon content influences transformation temperature as well as microstructural characteristics while alloying elements and cooling rate influence phase transformations, ultimately shaping final microstructure properties and material characteristics.
Applications of Bainite and Martensite in Industry
Bainite and martensite, two distinct microstructures formed of steel alloys, possess distinct properties that make them appealing in various industries for specific uses.
Applications of Bainite:
- Automotive Components: Bainitic steels have become an invaluable material choice in automotive component production due to their combination of high strength, toughness and good wear resistance properties – perfect for handling heavy loads and impact forces.
- Machinery and Structural Parts: Bainitic microstructures offer an optimal combination of strength, ductility, and fatigue resistance; making them an excellent choice for machinery components like shafts, bearings and structural parts that must remain reliable under dynamic loading conditions.
- Railways: Bainitic steels find widespread application in railway systems for producing durable and wear-resistant components like rails, wheels, and axles that meet long service lives with reduced maintenance needs.
Applications of Martensite:
- Cutting Tools: Martensitic steels are widely utilized to produce cutting tools like drills, saw blades, and machining inserts made of martensite; due to its hardness and wear resistance properties these cutting tools can withstand metalworking processes without becoming worn-down by repeated usage.
- Blades and Cutlery: Martensite stainless steels are highly-regarded materials used in making knives, blades, and cutlery items due to their hardness and edge retention properties, giving sharp cutting edges while enhancing durability.
- Springs: Martensitic spring steels possess superior elastic properties and maintain their shape under repeated loading and unloading cycles, which makes them popular choices for use in spring applications such as automotive suspension systems and industrial machinery.
What is the Difference Between Bainite and Martensite?
Here’s a concise comparison chart highlighting the key differences between Bainite and Martensite:
Aspect | Bainite | Martensite |
---|---|---|
Formation Mechanism | Diffusion-controlled transformation | Diffusionless transformation |
Crystal Structure | Ferrite + Cementite mixture | Tetragonal distortion of austenite |
Morphology | Acicular (needle-like) | Needle-like or lath-shaped structures |
Mechanical Properties | Improved toughness, ductility | High hardness, strength, brittleness |
Applications | Automotive parts, machinery | Blades, cutlery, springs, tooling |
Heat Treatment | Isothermal transformation, tempering | Quenching, tempering, reducing brittleness |
Formation Temperature | Intermediate temperatures | Rapid cooling from austenitic phase |
Crystal Lattice Change | Moderate distortion | Significant lattice distortion |
Transformation Kinetics | Slower rates | Rapid transformation kinetics |
Tempering | Less affected by tempering | Required for ductility and toughness |
Alloy Composition | Broad range of alloy compositions | Affected by carbon content, alloying |
Advantages and Disadvantages of Using Bainite and Martensite in Steel Production
Benefits of Utilizing Bainite in Steel Production:
- High Toughness: Bainite offers improved toughness when compared to martensite due to its slower transformation kinetics, making bainitic steel less susceptible to brittleness or cracking under impact or dynamic loading conditions. This makes them less vulnerable than martensite materials when applied as coatings on structural parts such as bridges.
- Strength-Ductility Balance: Bainite offers an ideal compromise between strength and ductility, making it suitable for applications involving mechanical stress as well as deformation.
- Wear Resistance: Banite’s fine acicular structure imparts it an outstanding wear resistance, making it suitable for applications involving heavy abrasive wear or sliding contact between components.
- Fatigue Resistance: Bainitic microstructures exhibit superior fatigue resistance, making them suitable for components subject to repeated loading cycles or sudden stress variations.
- Reduced Distortion: Bainite forms at intermediate temperatures, permitting slower cooling rates and reduced thermal distortion compared to martensite’s rapid quenching requirements.
Substantial Benefits and Drawbacks to Bainite Use:
- Slower Transformation Kinetics compared with Martensite: Because bainite formation relies on diffusion-controlled processes, its transformation kinetics tend to be slower compared with martensite’s, making rapid cooling and transformation impossible. This may present challenges during rapid cooling/transformation operations.
- Lower Hardness Level: Bainite tends to possess lower hardness levels compared to fully quenched martensite, restricting its application in situations that demand high levels of hardness.
Advantages of Martensite in Steel Production:
Martensite exhibits superior hardness and wear resistance due to its irregular crystal structure and high carbon content, offering exceptional hardness and wear resistance for any material used as wear-resistant components.
- High Strength: Martensite’s lattice distortion gives it its high strength, making it suitable for applications requiring load bearing capacity.
- Martensitic steel: Martensitic steels provide accurate cutting edges due to their ability to retain sharp cutting edges for extended periods.
- Heat Treatment Control: Rapid transformation to martensite allows for precise material property control through quenching and tempering processes, giving rise to precise heat treatment control of material properties.
Disadvantages of Martensite:
- Brittleness: Due to martensite’s combination of hardness and rapid transformation rate, its surface can become susceptible to cracking under sudden loads or under impact loads, putting it at risk of cracking and fracture.
- Martensitic Steels Have Limited Toughness: Martensitic steels tend to be less tough compared to bainitic steels, limiting their application in applications requiring impact resistance.
- Distortion and Cracking: Rapid cooling required for martensite formation can result in distortion and cracking for larger or complex-shaped components if they aren’t treated effectively during heat treatment.
Final Thoughts
Bainite and martensite are microstructures formed through distinct processes in steel. Bainite typically forms at intermediate temperatures and offers the right balance of strength, toughness, and wear resistance that makes it suitable for automotive and machinery components.
Martensite forms rapidly with higher hardness and strength but brittle characteristics making it suitable for cutting tools, blades, and high-strength applications; selecting between them depends upon desired properties as well as application needs.