A brief introduction to Austenitic and Martensitic Stainless Steel
The main distinction between Austenitic and Martensitic Stainless Steel lies in their respective structures; austenitic is one-sided while martensitic stainless steel features body-centered structures.
There are four broad categories of stainless steels based on their crystallization: austenitic ferritic martensitic and duplex. Their microstructure depends upon which alloying elements they contain and therefore have different alloying elements present within.
Definition of stainless steel
Stainless steel alloy is composed of steel that contains at least 10.5 percent chromium in mass making it one of the premier metals to resist corrosion chemical exposure, and environmental conditions.
Chrome creates an ultrathin oxide surface layer called a passive layer that acts as protection from corrosion – and even self-heals after any damage, giving stainless steel its exceptional resistance against staining, corrosion, and staining.
Alongside chromium, stainless steel may also incorporate other alloying elements like molybdenum, nickel, and copper that enhance its properties and create different grades and types of stainless steel with unique characteristics and uses. These alloying elements contribute to various grades and types of stainless steel which each have distinct applications and characteristics.
Stainless steel has become an indispensable material across various industries, from automotive and construction to food processing, aerospace medical, and others. Due to its flexibility, durability, and corrosion resistance, it makes stainless steel an excellent material choice for use in structural parts kitchen appliances, and surgical instruments.
Furthermore, its attractive properties make it appreciated due to various methods of surface treatment available such as polishing, brushing, or etching that create desired aesthetic effects.
Importance of stainless steel in various industries
Stainless steel plays a crucial role in various industries due to its numerous advantages and properties.
Some of the key reasons why stainless steel is important in these industries are:
1. Corrosion Resistance: One of stainless steel’s primary advantages is its excellent resistance to corrosion. Able to withstand exposure to chemicals, moisture and harsh environments, stainless steel is widely used in industries that rely on corrosion prevention such as marine gas processing, oil chemical processing and water treatment, making it suitable for harsh environments like these.
2. Hygiene and sanitation: This product is ideal for businesses that adhere to stringent sanitation and hygiene standards, such as food manufacturing companies, pharmaceutical firms, health facilities or laboratories where sterility and sanitation is critical. It makes cleaning effortless. Not porous either – making this ideal for any environment where hygiene and sterility is a top priority such as hospitals or laboratories where cleanliness are key elements.
3. Strength and Durability: Stainless steel is a strong, versatile material with great tensile strength and resistance to impact, capable of withstanding high loads, temperatures and mechanical strain – qualities which make it suitable for applications including auto manufacturing, aerospace engineering, structural design construction projects as well as marine applications.
4. Fire and Heat Resistance: Stainless steel has remarkable fire and heat resistance properties that allow it to maintain its durability and strength in environments with extreme temperatures, such as energy generation or furnace manufacturing, where exposure to such extreme conditions could present serious risks. Consequently, this metal has found widespread application.
5. Aesthetic Attractiveness: Stainless steel’s appealing appearance and ability to be refinished with various treatments has made it popular with industries that prize aesthetics, from decorative elements and interior design projects to consumer goods that boast modern, appealing looks.
6. Environmental Sustainability: Stainless steel is an extremely eco-friendly material. It can be recycled 100% without losing quality, thus decreasing raw material extraction requirements and energy use during the manufacturing of stainless steel, making recycling more Sustainable than manufacturing directly.
7. Versatility: Stainless steel offers versatility due to its variety of finishes and grades, each providing different mechanical properties, resistance to corrosion, aesthetic options, and mechanical strength properties. This allows it to meet industry-specific demands as well as be applicable across various fields and applications.
Stainless steel’s corrosion resistance, durability, strength aesthetics, and environmental durability make it an essential component in many industries including construction, transport, food processing, energy supply, healthcare, and others. Today it serves to ensure safety efficiency and durability across multiple fields.
Classification of stainless steel into different grades
Stainless steel is classified into different grades based on their composition, properties, and specific applications.
The two most commonly used classification systems for stainless steel grades are:
1. Classification by AISI/SAE:
American Iron and Steel Institute (AISI) and Society of Automotive Engineers (SAE) have come up with a system for categorizing graded stainless steel grades using numbers. Under this system, grades of stainless steel are identified using three-digit numerals wherein their primary numeral indicates series, or general kind of the stainless steel material.
- Austenitic Stainless Steels (Series 200 and 300): The Austenitic series (311, 304, and 316) are among the most commonly utilized and flexible stainless steel grades, featuring high levels of nickel and chromium for exceptional corrosion resistance, conductivity, shapeability and non-magnetic characteristics. Austenitic stainless is non-magnetic making them popular choices across various industries including food processing chemical architecture.
- Ferritic Stainless Steels (Series 400): The grades in this series (e.g. 446, 4, and 433) contain chrome as their primary alloying element for corrosion protection and moderate strength with magnetic properties, making these ferritic stainless steels widely utilized for exhaust systems of automobiles as well as heat exchangers and other appliances.
- Martensitic Stainless Steels (Series 400): Grades from this series (e.g. 403, 420, 440 and 410 respectively) contain high concentrations of carbon with moderate or high levels of chrome, providing outstanding hardness, strength and wear-resistance properties that make Martensitic stainless Steels popular choices for surgical instruments as well as industrial applications requiring toughness and corrosion resistance.
- Precipitation Hardening Stainless Steels (PH Grades): These grades (e.g. 17-4PH 15-5PH 17-4PH) can be hardened through heating treatment to achieve high levels of strength. They offer great corrosion resistance as well as exceptional mechanical characteristics, making them suitable for chemical processing, aerospace applications, or any other demanding uses that demand high performance.
2. UNS (Unified Numbering System) Classification:
Developed by ASTM (American Society for Testing and Materials), the UNS system assigns each stainless steel type a unique alphanumeric code. These UNS codes feature “S” followed by a number identifying its type (e.g. “S30400 for AISI 304) along with its grade designation number and numeric grade designation code.
The UNS system offers an exhaustive classification of stainless steel grades, including ferritic and austenitic martensitic duplex precipitation hardening grades and specific alloy variants.
Keep in mind that different standards bodies use various classification systems, including EN (European Standard), JIS (Japanese Industrial Standards), as well as others such as the AISI/SAE or UNS classifiers to classify stainless steel. However, these classification systems have become widely accepted methods to classify it.
What exactly is Austenitic Stainless Steel?
Austenitic stainless steel can be described as an alloy composed of the metal stainless steel which exhibits resistance to corrosion, as well as superior mechanical properties. The basic crystal structure for austenitic stainless steel alloy is face-centered cubic structure.
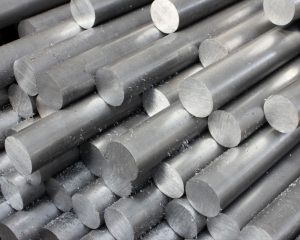
Furthermore, this alloy includes “austenite”, which is an iron-based solid solution which contains some alloying elements (and may also act as its binding element).
Additionally, these materials offer increased strength, toughness, flexibility and formability compared to their counterparts. Furthermore, these materials can withstand both cryogenic (low temperature) and high-temperature processes as well as aesthetic appeal; their structure resembles an asymmetrical cubic cube that features one Atom at each corner plus one Atom on every face (at its center).
Structure is formed when sufficient amounts of nickel, chromium, and iron combine. A typical composition for such material would contain around 15% chromium along with 8-10 percent nickel.
What exactly is Martensitic Stainless Steel?
Martensitic stainless steel can be broadly defined as an alloy with more chromium but no nickel present, with high or low carbon content depending on carbon levels in its formulation. Furthermore, its composition consists of 12 percent iron, 17% chromium, 0.10 percent carbon content.
Key features of martensitic stainless steel include its mechanical property and wear resistance properties. Martensitic crystal is a body-centered cubic structure. Each corner of this cube contains one atom while one more sits centered in its core.
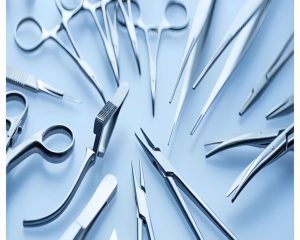
Fundamentally, there is no nickel present in this material and its characteristics include being ferromagnetic with heat treatments allowing hardening as well as less corrosion resistance than its counterparts.
Difference Between Austenitic and Martensitic Stainless Steel
Austenitic and Martensitic Stainless Steel are two distinct varieties of stainless steel that differ significantly in terms of their structure, composition, properties and applications.
Here are the primary differences between martensitic and austenitic varieties:
1. Crystal Structure of Austenitic Stainless Steel:
A. Austenitic Stainless Steel: Austenitic stainless steels feature an FCC crystal structure which gives it excellent durability and ductility, as well as thermal stability over an expansive temperature range.
B. Martensitic Stainless Steel: Martensitic stainless steel can be identified by its body-centered cubic (BCC) crystal structure when in its annealed state, but after quenching this structure transforms into reinforced martensitic structure which results in increased toughness and decreased ductility.
2. Carbon Content of Austenitic Stainless Steels:
A. Austenitic Stainless Steel: Austenitic stainless steel is distinguished by containing minimal amounts of carbon – typically below 0.08 percent – while emphasizing high nickel and chromium concentrations to achieve corrosion resistance as well as enhance mechanical properties.
B. Martensitic Stainless Steel: Martensitic stainless steels contain more carbon, typically between 0.1% to 1.2%. This higher level of carbon contributes to martensite formation which enhances toughness and strength of this variety of steel.
3. Mechanical Properties:
A. Austenitic Stainless Steel: Austenitic stainless steel has exceptional ductility, high toughness and excellent shapeability; however it has less hardness than its martensitic counterpart.
B. Martensitic Stainless Steel: Martensitic stainless steel stands out by its strength hardness and resistance to wear. With superior hardness and strength when compared with austenitic stainless steels, martensitic stainless steels make an excellent choice for applications requiring top mechanical performance.
4. Corrosion Resistance:
A. Austenitic Stainless Steel: Austenitic stainless steel provides exceptional corrosion resistance due to its high nickel and chromium content, creating a protective oxide layer which acts as a buffer against corrosion under various environmental conditions.
B. Martensitic Stainless Steel: Martensitic stainless steel provides moderate corrosion resistance. However, due to its lower content of chromium it may not last as long.
5. Magnetic Properties:
A. Austenitic Stainless Steel: No magnetic properties exist when austenitic stainless steel is in its an annealed condition, although certain conditions can induce it to exhibit these features.
B. Martensitic Stainless Steel: Martensitic stainless steel has an attractive magnetic property due to its crystal formation and increased carbon content, creating a magnetic attraction.
6. Applications:
A. Austenitic Stainless Steel: As one of the premier corrosion resistant materials available today, austenitic stainless steel finds its application across several industries, such as food processing plants, chemical processes and medical and architectural equipment where formability, hygiene and corrosion resistance are key considerations.
B. Martensitic Stainless Steel: Martensitic stainless steel can be found in numerous industries that demand strength, hardness and wear resistance properties of their materials, such as cutting boards, knives and cutlery for cutlery; turbine and compressor components automotive components as well as equipment used in petrochemical plants.
Understanding these distinctions is vital when selecting the appropriate quality of stainless steel to meet individual requirements based on desired properties and performance requirements.
Comparison Chart of Austenitic and Martensitic Stainless Steel
Here’s a chart that highlights the main differences between Austenitic and Martensitic Stainless Steel:
Aspect | Austenitic Stainless Steel | Martensitic Stainless Steel |
---|---|---|
Crystal Structure | The face-centered cubic (FCC) | Bodies-centered cubic (BCC) is transformed into martensite when quenched. |
Carbon Content | Carbon content is low (<0.08 percent) | Carbon content higher (0.1% to 1.2 percent) |
Mechanical Properties | High ductility, excellent ductility Lower strength and harderness | Strong, toughness and wear resistance |
Corrosion Resistance | Excellent corrosion resistance | Moderate resistance to corrosion but not as strong as austenitic |
Magnetic Properties | Non-magnetic in the annealed state could be slightly magnetic following cold-working | Carbon content and structure of crystals. |
Applications | Chemical processing, food processing Architectural applications medical equipment | Blades, cuttinglery, turbine parts, automotive components, and other automotive |
Formability | Formability is excellent. | Formability and ductility are lower as well as less ductile in comparison to austenitic |
Heat Treatment | Unabsorbable after the use of heat | It is hardenable through heating treatment, changing into martensite |
Common Grades | 304, 316, 321, 904L | 410, 420, 440C, 17-4PH, 15-5PH |
Selection Factors and Considerations
When selecting between Austenitic and Martensitic Stainless Steel, several factors and considerations should be taken into account.
These include:
1. Corrosion Resistance: When considering how stainless steel will be utilized, keep corrosion resistance in mind. Austenitic stainless steel typically offers the greatest corrosion protection against chloride- and acidic environments, so if the work involves exposure to potentially corrosive substances or extreme conditions then austenitic stainless may be your go-to material choice.
2. Strength and Hardness of Material: Evaluate the required mechanical properties before selecting material. Martensitic stainless steel offers greater toughness and strength compared to austenitic stainless steel for use in demanding jobs that demand strong durability, strength or hardness and hardness requirements; for this reason it could be an ideal solution.
3. Weldability and Strength: Consider all necessary requirements of fabrication before beginning your project. Austenitic stainless is highly malleable and welds easily, making it suitable for intricate designs. Martensitic steel tends to be less malleable and requires more effort when welding; hence austenitic is often preferred when large welding or shaping needs to take place.
4. Magnetic Properties: Consider what magnetic qualities would be useful or not suitable for the task at hand. Usually non-magnetic austenitic stainless is preferred while martensitic steel boasts magnetic qualities – however certain industries or fields might need specific magnetic requirements for certain jobs or tasks.
5. Cost: Carefully consider the financial implications of the project. Due to its higher nickel content, austenitic stainless steel tends to cost more than martensitic varieties; therefore, take your budgetary constraints and performance requirements into account when making this determination.
6. Temperature Resistance: To select an austenitic stainless steel for applications requiring temperature resistance, keep in mind the desired temperature range for that application. It will maintain toughness and ductility at both low and high temperatures while martensitic stainless steel may show less ductility or toughness at lower temperatures.
7. Special Application Requirements: Identify any special application requirements or standards which must be fulfilled for this application. Certain industries, like food processing or healthcare sectors, may have specific regulations regarding using stainless steel.
8. Services and Maintenance Lifespans: When considering the requirements and anticipated lifecycle of stainless steel, take note of both its maintenance requirements as well as expected lifespan. Austenitic stainless steel usually requires less attention due to its resistance to corrosion; on the other hand, martensitic varieties might require more effort to prevent corrosion and preserve performance.
Consider these factors and consult with professionals or engineers, to make the right selection of stainless steel that meets all of the project requirements in terms of corrosion resistance, mechanical properties, fabrication specifications and cost considerations.
Conclusion
Martensitic and austenitic varieties of stainless steel each possess distinct properties and applications, with martensitic being more corrosion-resistant while austenitic boasting greater formability, making it more suitable for architectural uses than its martensitic counterpart.
Austenitic stainless is popularly used due to its face-centered cubic structure which boasts excellent corrosion resistance as well as increased ductility. These qualities make it popular across various industries including food processing and chemical processing while architectural applications may also benefit.