An Introduction to Zirconia and Aluminum Oxide
Aluminum oxide and zirconia ceramics are two widely utilized ceramic materials due to their distinct features, making them integral parts of many industries.
Here is an Introduction for each ceramic:
Zirconia: (zirconium dioxide, more commonly referred to by its initials ZrO2) is an exceptional ceramic material renowned for its strength, durability and heat conductivity properties.
Derived from zirconium silicate minerals through sintering processes to obtain its desirable characteristics, Zirconia boasts superior mechanical properties such as hardness, fracture strength resistance, and wear resistance while possessing outstanding chemical stability and corrosion resistance properties – qualities it owes its famed mechanical qualities.
Applications for Zirconia include dental prosthetics/implants as well as high-temperature components/oxy sensors.
Aluminum Oxide: Aluminium oxide (Al2O3), also referred to as Alumina or Al2O3, is an extremely useful ceramic that finds widespread industrial usage.
Produced by calcining bauxite ore into aluminum oxide through the process of calcination, aluminum oxide possesses excellent hardness, wear resistance, and chemical stability characteristics which makes it popularly utilized as an abrasive in polishing, grinding, or surface finishing processes as well as being employed as ceramic coating material, electric insulation material or composite filler material in composite manufacturing processes.
Zirconia and oxide share certain properties related to ceramic properties and nature; however, their composition, crystal structure, and specific properties vary significantly – it’s essential that you understand these differences to select an effective material for your particular application needs.
Importance and applications of Zirconia and Aluminum Oxide
Zirconia and Aluminum Oxide are key ceramic materials with numerous uses across multiple industries, so here is some information regarding both materials:
Zirconia:
1. Dental Implants and Prosthetics: The zirconia material’s biocompatibility, strength, and attractive appearance make it the go-to material for dental implants as well as prosthetic crowns and bridges, featuring long-term restoration that looks natural compared to metal alternatives. Additionally, its excellent mechanical properties offer long lasting restoration solutions.
2. Applications at High Temperatures: Zirconia exhibits impressive thermal resistance, making it suitable for environments where temperatures reach extreme levels. Applications that make use of its exceptional qualities include thermal barriers, heating components and even melting metals with its help.
3. Oxygen Sensors: Zirconia sensors are often utilized by industrial and automotive applications for monitoring oxygen levels in industrial settings or vehicle cabins, due to their reliable detection. Zirconia features high ionic conductivity at temperatures which allows accurate oxygen detection.
Aluminum Oxide:
1. Abrasives and Polishing: Aluminum oxide is widely utilized as an abrasive material to grind cutting, polishing and cutting applications on wood, metal, other surfaces such as ceramic tile etc. Aluminum oxide also finds use as an ingredient of polishing chemicals used on these surfaces such as furniture wood grain floors etc.
2. Ceramic Coatings: These ceramic coatings made of aluminum oxide provide superior corrosion, wear and heat protection in many applications, such as engine components or cutting tools that rely on them, surface protection against wear or surface protection against damage caused by wear-and-tear, as well as engine component coatings against corrosion or wear and heat protection. They’re often employed on cutting tools as surface protection against wear.
3. Electrical Insulators: Aluminum oxide’s powerful dielectric strength and thermal stability make it an invaluable material in the electrical industry, being widely utilized to construct various elements like electronic boards or high voltage equipment.
4. Catalyst Supports: Aluminum oxide serves as an invaluable catalyst support material in several chemical processes. It offers durable and highly surface-area catalysts used for petroleum refining, chemical synthesis and environmental applications.
Zirconia and aluminium oxide both possess unique characteristics which make them useful in specific fields, from dentistry and aerospace through automotive production and electronics production. Their performance characteristics have played a large part in innovation within various industries including dentistry, aerospace manufacturing and electronics development.
What exactly is Zirconia?
Zirconia (zirconium oxide) is an oxide-based inorganic compound with the formula ZrO2. Also referred to as zirconium dioxide, this element has two oxygen atoms for every zirconium atom within each molecule and forms white crystals with monoclinic crystal forms.
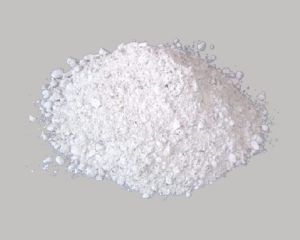
Zirconia gems of various hues can now be made by calcining zirconium compounds with high thermal stability to make cube-structured zirconia gems of any desired shade.
Additionally, this compound can be found in three different crystal structures with different temperatures: monoclinic, cubic and hexagonal. Of the three forms available to us today, monoclinic crystal structure is by far the most stable and natural form – even acidic chemicals like H2SO4 or HF may slowly take hold over time and take over this natural substance.
Heat will change this compound into zirconium carbide; when mixed with chlorine it forms zirconium Tetrachloride which provides the basis for purifying zirconium. This reaction provides the basis of purifying zirconium.
Zirconia finds widespread application in ceramic manufacturing processes; as an insulator; for enamels and abrasives; or due to its high ionic conductivity as an electroceramic material.
What exactly is Aluminum Oxide?
Aluminum oxide compound (Al2O3) is one of the most resilient and natural forms of aluminium oxides, being an organic oxide with the formula Al2O3.
We call alumina aluminum oxide. A natural compound found in its crystallized state as alpha polymorphic phase crystal, it forms transparent solid with trigonal crystal structure and shape; corundum being one of its natural forms.
Assessing this compound reveals its capabilities: an excellent electrical insulator which dissolves with water but remains weather resistant; additionally it protects aluminum metal’s surface from further corrosion while functioning as an amphoteric compound.
Acid and bases react with it to cause neutralizing reactions that benefit both water and salt.
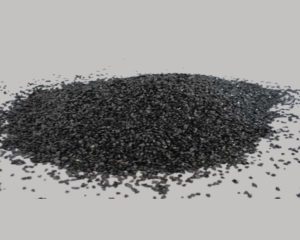
Aluminum oxide can be utilized for numerous uses:
- As a Refractory Material
- For ceramic and Abrasives production.
- To fill plastics. unplug glass as an ingredient
- To isolate gas streams that contain water.
- Chemical reactions using Methylene Chloride as a catalyst. It plays an essential role in organic synthesizing reactions.
- Used as an ingredient in paints and coatings.
Difference Between Zirconia and Aluminum Oxide
Here is the key difference between Zirconia and Aluminum oxide in below:
Composition and Structure of Zirconia
Zirconia (ZrO2) more commonly referred to by its alternative name of zirconium dioxide (ZrO2) is composed of zirconium and oxygen atoms bonded together into an organic compound each zirconium particle combining two oxygen atoms to produce one Zirconia atom hence forming its chemical formula ZrO2.
Zirconia crystal structure may vary based on temperature and impurity content; when at room temperature it commonly forms monoclinic structures; at higher temperatures however it transforms further and displays cubic and tetragonal phases as it undergoes phase transformations.
Zirconia crystal structure plays a profound influence over its properties. Tetragonal and cubic phases of zirconia possess higher strength and toughness compared to monoclinic phases; this phenomenon is known as transformation or “transformation toughening”, in which changing one crystal structure into the next helps prevent crack propagation while increasing mechanical properties.
Aluminum Oxide Composition and Structure Aluminium oxide, more commonly referred to as Alumina (Al2O3) is composed of oxygen and aluminum atoms bound together into molecules by bonds of three oxygen atoms between each two aluminum atoms that come together with three aluminum atoms in its chemical formula: Al2O3.
Aluminum oxide crystal structure comprises oxygen ions tightly packed together with aluminum ions in their spaces between oxygen ions forming what are known as corundum structures – these are defined by an oxygen lattice composed of hexagonal close packing hexagonal filled with aluminum ions taking up several of its octahedral.
Tetrahedral sites in close-packing hexagonal hexagons arranged octahedra or Tetrahedra sites within hexagonal cells of hexagonal lattice structure that also contains many aluminum sites where aluminum takes over several spots within hexagonal lattice structure itself defining corundum structures as corundum structures a mineral compound of great interest due.
Their physical characteristics and appearance when found inside of these corundum crystal structures they are often called corundum structures, due to being tightly packed together and their use within these corundum structures being defined by their hexagonal close packed hexagonal lattice cells containing many aluminum ions taking several octahedral.
Tetrahedral sites within hexagonal lattice lattice sites in lattice structure defined. This structure typically known as corundum structures is defined by its hexagonal close packed hexagonal lattice defined by hexagonal close packed hexagonal lattice, comprising close packed hexagonal oxygen lattice defined by hexagonal close packed hexagonal lattice where aluminum takes several octana Lattice.
Aluminum oxide stands out due to the unique arrangement of its atoms within its crystal structure, giving it exceptional toughness, mechanical strength and thermal stability. Due to this precise alignment between oxygen and aluminum atoms in aluminum oxide crystal, its unique properties enable its use across a range of applications from ceramics to abrasives.
Zirconia consists of zirconium and oxygen atoms and features various crystal structures including monoclinic, tetragonal and cubic phases. Aluminium oxide contains aluminum as well as oxygen atoms in its crystal form commonly referred to as corundum; their composition and structures play an integral part in their properties and suitability for applications.
Physical Properties
Zirconia:
1. Hardness: It is an exceptionally durable and hard-wearing material with excellent resistance against wear and scratching, boasting Mohs hardness ratings of eight-9 on its scale – similar to sapphire or diamond in terms of its hardness.
2. Density: Zirconia crystal has an average density between 5.5-6 grams/cubic centimeter. However, depending on its composition or crystal structure this could change dramatically.
3. Melting Point: Zirconia boasts one of the highest melting points, at approximately 2715degC (4,919degF). This melting point ensures zirconia remains structurally sound even at elevated temperatures.
4. Thermal Conductivity: Zirconia boasts an extremely low thermal conductivity when compared with other metals, generally between 2-3% Watts Per Meter-Kelvin (W/m*K), making it an effective insulator in applications featuring higher temperatures.
Properties of physical Aluminum Oxide:
1. Hardness: The aluminum oxide material is well known for its impressive hardness; Mohs scale rates it as hard as corundum! Hence it makes an exceptional tough material.
2. Density: Aluminium oxide has an extremely high density typically between 3.9 to 4.1 grams per cubic Centimeter. This density depends upon factors like its purity as well as crystal structures within its crystals.
3. Melting Point: Aluminum oxide has an extremely high melting point that ranges between 2,040deg Celsius (3,704degF). This allows it to withstand even extreme temperatures without melting away in excess of this threshold temperature.
4. Temperature Conductivity: Aluminium oxide exhibits exceptional thermal conductivity when compared with other ceramics, typically 20-40 W/m*K for efficient heat transfer in areas that demand management of thermal energy.
Zirconia and aluminum oxide physical characteristics will depend heavily on factors like composition, crystal structure and processing techniques, which will have an impactful impact on their physical characteristics and determine suitability for particular applications – for instance their capacity to endure extreme temperatures, endure wear or provide thermal insulation.
These physical properties play a pivotal role in material choice decisions for applications including thermal insulation.
Mechanical Properties
Zirconia:
1. Strength: Zirconia boasts high strength properties that make it ideal for projects requiring resistance against mechanical strains. However, depending on its crystal structure and composition this strength may change accordingly.
2. Toughness to Fracture: Zirconia has outstanding fracture toughness, meaning it can resist propagation of cracks while withstanding impact and applied forces without catastrophic failure. This characteristic is due to phase transformation which occurs as zirconia undergoes changes to its crystal structure during stress conditions.
3. Wear Resistance: Zirconia is widely recognized for its outstanding wear resistance, making it suitable for applications involving forces of erosion or abrasion. This feature can be attributed to both its toughness and wear resistance properties.
Mechanical properties of Aluminum Oxide:
1. Strength: Aluminum oxide has strong mechanical strength that allows it to resist mechanical forces as well as deformation. Its strength depends on factors like purity of its crystal structure and grain size.
2. Resistance to Fracture: Aluminum oxide has high strength against fracture, making it suitable for impact protection and crack resistance, though its fracture toughness typically falls shorter than with zirconia.
3. Wear Resistance: Aluminum oxide is well known for its superior wear resistance. Thanks to its toughness and ability to retain surface strength even under harsh abrasive conditions, aluminum oxide makes for the perfect material in applications which involve contact between hard materials or surfaces such as granite.
Both zirconia and aluminium oxide exhibit outstanding mechanical properties that make them suitable for many different applications, especially ones where toughness, strength and wear resistance are critical elements.
Their exact physical and mechanical characteristics vary based on factors including composition of material crystal structure processing techniques as well as any additives which might be added during their processing and additive use.
Chemical Properties
Chemical properties of Zirconia:
1. Resistance to Corrosion: Zirconia stands out as an excellent corrosion-resistant material in alkaline and acidic environments alike, resisting chemical attack by bases, acids and solvents without succumbing to degradation from these agents. Zirconia offers great chemical stability where its resilience against corrosion is vital.
2. Chemical Stability Chemical Stability: Zirconia’s stability chemically makes it ideal for high temperatures as well as extreme environments, not experiencing major chemical reactions or degrading during normal operation conditions, thus helping preserve both its structure and properties over time.
Chemical properties of Aluminum Oxide:
1. Corrosion Resistance: Aluminum oxide has excellent corrosion resistance properties against acids and bases, creating an oxide protective film known as Alumina that stops further degradation or corrosion to material surfaces.
2. Chemical Stability: The material is chemically stable and doesn’t react with most common chemicals in normal circumstances, making it suitable for applications that demand stability during chemical processes. It maintains its properties and integrity under changing chemical environments – making it the perfect material choice.
Zirconia and aluminum oxide materials are known to be chemically stable and resist corrosion; their particular chemical properties,
However, may be altered depending on certain environmental or climate-related factors like impurities present, temperature or the presence of particular chemical compounds – thus it’s vital that users consider all conditions involved when selecting appropriate materials for any given task.
Applications
Applications of Zirconia:
1. Dental Implants and Prosthetics: Zirconia’s biocompatibility, strength, and aesthetic appeal make it an ideal material for dental implants, crowns, bridges, and dentures. It offers excellent durability and natural-looking results.
2. Highly-Temperature Materials: Zirconia’s large melting points and thermal stability make it the ideal material for applications involving high temperatures, including automotive, aerospace and power generation industries for creating components like thermal barriers, furnace coatings and crucibles.
3. Oxygen Sensors: Zirconia sensors that monitor oxygen levels can be found in automotive combustion systems, industrial processes and medical settings to provide accurate measurements that allow accurate, reliable measurements. These sensors make an ideal addition for applications involving automotive emissions monitoring or medical oxygen needs monitoring systems.
Application of Aluminum Oxide:
1. Abrasives and Polishing: Aluminium oxide is widely utilized as an abrasive material in grinding or sanding applications, often employed within wheels, sandpaper and polishing compounds for metals glass ceramics and wood surfaces.
2. Ceramic Coatings: Aluminum oxide-based ceramic coatings offer exceptional corrosion, wear and heat protection in various applications such as engine parts coatings or wear-resistant surfaces on cutting tools and wear resistant surfaces. They have become an essential solution.
3. Electrical Insulators: Aluminum oxide’s combination of high dielectric strength and thermostability make it the ideal material to insulate electrical power from leakage, making it popularly employed as insulation material in components, circuit boards and high voltage applications.
4. Catalyst Supports: Aluminium oxide serves as catalyst support material in various chemical processes. As it offers solid support with high surface area coverage for catalysts used for petroleum refining chemical synthesis as well as environmental applications, aluminium oxide makes an excellent catalyst support material choice.
Both zirconia and aluminum oxide find wide use across industries such as dentistry, aerospace manufacturing and electronics production. Their versatile characteristics make them useful in specific applications requiring strength as well as high temperature resistance, wear resistance and chemical stability.
Pros and Cons
Pros and Cons of Zirconia:
Pros
1. Zirconia Is Strong and Durable: Zirconia boasts exceptional strength and durability, providing resistance against mechanical stress while decreasing chances of breakage or failure.
2. Biocompatibility: Zirconia has demonstrated excellent biocompatibility with human bodies and therefore it has found extensive use as dental implants and prosthetics material.
3. Corrosion Resistance: Its high resistance to corrosion. Zirconia boasts outstanding resistance against corrosion, making it suitable for applications which expose it to alkalis, acids or harsh chemicals such as alkalines or acids.
4. Aesthetic Appeal: Zirkonia can be designed to look just like natural teeth, making it an attractive material for dental restorations thanks to its natural aesthetic.
Cons:
1. Price: Although Zirconia tends to be more costly than other dental materials, this could pose challenges in certain applications.
2. Machining: Zirconia is an extremely hard material that makes shaping and machining it challenging; in order to do this effectively requires specific equipment and methods.
3. Low Thermal Conductivity: Zirconia has low thermal conductivity, making it unsuitable for processes requiring efficient heat transfer at high temperatures.
Pros and Cons of Aluminum Oxide:
Pros:
1. High Hardness and Wear Resistance: Aluminum oxide is widely recognized for its hardness and wear resistance properties, making it suitable for applications requiring abrasives as well as durable components that must last over time.
2. Corrosion Resistance: Aluminum oxide forms an oxide protective layer to provide better corrosion protection, making it the perfect material to use in environments susceptible to corrosion.
3. Thermal Stability: Aluminum oxide’s thermal stability enables it to withstand high temperatures without major degradation, making it an excellent material choice for applications that demand such conditions.
Cons:
1. Brittleness: Aluminum oxide can be fragile under certain circumstances. In particular, large impact forces could result in it shattering easily and breaking.
2. Low Electrical Conductivity: Aluminium oxide can act as an electrical conductor and may therefore not be suitable for Applications requiring such conductivity.
3. Cost: Aluminum oxide may be more costly than alternative materials and less suited to budget-sensitive projects than alternatives such as paper.
Note that any benefits or drawbacks mentioned above should only be seen as generalized considerations; specific outcomes depend on processing method, application needs and various other considerations.
When making this choice between zirconia or aluminum oxide for any given application it’s essential that all characteristics match up perfectly to meet any limitations that might exist within that industry or field of application.
Study Comparing Zirconia and Aluminum Oxide: Comparative Evaluation
1. Composition: Zirconia consists of oxygen and zirconium atoms (ZrO2) while aluminum oxide contains oxygen atoms as well as aluminum (Al2O3) – these two materials make up their composition respectively.
2. Crystal Structure: Zirconia can form into multiple crystal structures depending upon temperature and impurity levels; such as monoclinic, tetragonal and cubic phases depending upon temperature and impurities. Aluminum oxide forms into an elongated crystal structure often known as corundum due to its hexagonal oxygen lattice with interstitial sites for aluminum ions occupying them.
3. Mechanical Properties: Both zirconia and aluminum oxide exhibit excellent wear-resistance and toughness properties, though zirconia’s higher strength-toughness ratio enables it to withstand crack propagation more readily; aluminum oxide offers slightly greater fracture toughness but more fragility.
4. Physical Properties of Thermal: Zirconia has lower thermal conductivity than aluminum oxide, making it an effective heating conductor. While aluminum oxide’s good thermal conductivity could provide great heating capability in certain instances, Zirconia could prove invaluable for situations that necessitate thermal insulation.
5. Chemical Properties: Zirconia and aluminum oxide both offer outstanding resistance to corrosion. Zirconia in particular stands up well to chemical attacks while still remaining chemically stable at higher temperatures; aluminum oxide forms an oxide protective layer to further increase this property; however, zirconia proves more stable over its lifecycle than aluminium oxide.
6. Applications: Zirconia has numerous uses in prosthetics and dental implants as well as high-temperature components and oxygen sensors, while aluminum oxide can be found in ceramic coatings, abrasives electrical insulators, catalyst supports, and other ceramic applications. Both materials find wide application in fields including dentistry and aerospace as well as automotive and manufacturing.
7. Cost: Zirconia tends to be more costly than aluminum oxide and this could influence its price and suitability for specific applications.
Before selecting zirconia over aluminum oxide for any specific application, it’s vitally important to take into account all applicable criteria, including thermal conductivity, mechanical strength and chemical resistance requirements, cost considerations as well as any special considerations specific to that field of work.
Each material comes with unique benefits and drawbacks; choosing which is ideal depends upon weighing these against its limitations in relation to any proposed use of either one of them.
Conclusion
Aluminum oxide and zirconia are multipurpose materials with unique characteristics and uses. Of the two materials, zirconia stands out for its outstanding combination of strengths, toughness, biocompatibility and corrosion resistance that make it suitable for implants in dentistry as well as high-temperature parts like high-temperature parts for high-temperature engines and oxygen sensors.
Aluminum oxide, however, boasts exceptional hardness characteristics as well as corrosion, wear, and thermal stability – qualities which make it suitable for applications including ceramic coatings, abrasives electrical insulators, and catalyst supports.
Zirconia offers higher strength and toughness compared to aluminum oxide; however, aluminum oxide boasts greater thermal conductivity. Zirconia typically is more chemically stable at high temperatures while aluminum oxide acts as an oxide protective layer against corrosion.
Zirconia or aluminum oxide should be chosen depending on your application requirements – including thermal conductivity, mechanical strength, and chemical resistance as well as cost considerations – along with any specific advantages or disadvantages they present for either material.
It’s crucial that we evaluate both options carefully in order to select the one most suited to our intended use.
Zirconia and aluminum oxide offer various desirable characteristics, making them useful across a range of industries.
By understanding their structure, composition, physical and chemical properties as well as any potential advantages or disadvantages they can help make educated choices regarding selecting an optimum material for any task at hand.