Lead Chamber and Contact Process are two significant methods utilized in the industrial production of sulfuric acid. Sulfuric Acid is an indispensable industrial chemical with numerous applications and usage scenarios. We will delve into the Lead Chamber Process and the Contact Process, exploring their history, mechanisms, and differences.
What is the Lead Chamber Process?
The Lead Chamber Process is an older method used for the industrial production of sulfuric acid, one of the most important and widely used chemical compounds in various industries. In the 18th century, commercial sulfuric acid production first gained widespread use. The process was later replaced by the more efficient Contact Process, but its historical significance remains noteworthy.
Lead Chamber Process relies on a mixture of sulfur dioxide (SO2), water (H2O), as well as nitric dioxide or nitrous oxide. Producing sulfuric (H2SO4) acid requires an intricate series of reactions.
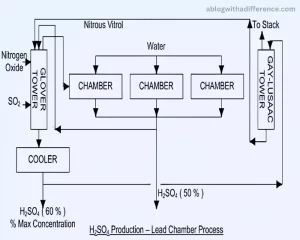
Here are the key steps involved in the Lead Chamber Process:
1. Combustion of Sulfur: Elemental sulfur (S) is burned to produce sulfur dioxide (SO2) gas. This can be achieved by burning sulfur or certain sulfur-containing minerals like pyrite (FeS2).
S + O2 → SO2
2. Sulfur Dioxide Absorption: Create sulfuric acid by mixing sulfur dioxide with water. The absorption of SO2 occurs in large chambers made of lead or lined with lead, hence the name “Lead Chamber Process.”
SO2 + H2O → H2SO3
3. Catalytic Oxidation: Nitric oxide (NO) or nitrogen dioxide (NO2) is introduced into the chambers. Nitro Oxides act as catalysts in the transformation of sulfurous acid H2SO3 to sulfuric acid H2SO4, providing an acidity gradient for conversion purposes. While performing this conversion process, nitrogen oxides will be transformed into nitric dioxide.
H2SO3 + NO → H2SO4 + NO2
4. Sulfuric Acid Formation: Step four is designed to increase sulfuric (H2SO4) acid in the chamber by reacting it further with water vapor.
H2SO4 + H2O → H2SO4(aq)
The process is cyclical, and the sulfuric acid concentration gradually increases over time. It is collected as a liquid from the bottom of the chambers. The spent gases containing nitrogen oxides and unreacted sulfur dioxide are recycled back to the process, and fresh air is introduced to ensure a continuous reaction.
While the Lead Chamber Process was historically significant and served as a crucial method for sulfuric acid production, it had several drawbacks, including low sulfur dioxide conversion efficiency, limited plant capacity, and environmental concerns due to the release of nitrogen oxides. As a result, the more efficient and environmentally friendly Contact Process eventually replaced it as the dominant method for sulfuric acid production in modern times.
What is the Contact Process?
The Contact Process is the modern and widely used method for the industrial production of sulfuric acid (H2SO4). Unlike the older Lead Chamber Process, the Contact Process is highly efficient and allows for the large-scale production of sulfuric acid with a higher concentration. This method is one of the most frequently employed for producing sulfuric acid globally.
The Contact Process involves a series of chemical reactions, including oxidation and absorption steps, which ultimately lead to the formation of concentrated sulfuric acid. The process requires specific conditions and a catalyst to promote the desired reactions.
The main steps involved in the Contact Process are as follows:
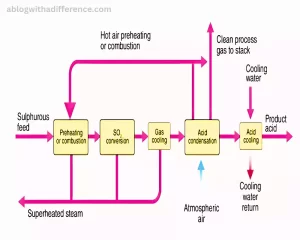
1. Combustion (or Production of Sulfur Dioxide): Sulfur dioxide can be produced via its first combustion (S). Alternatively, sulfur dioxide can be obtained from other sulfur-containing compounds or byproducts from various industrial processes.
S + O2 → SO2
2. Sulfur Dioxide Oxidation: The generated sulfur dioxide is then passed over a catalyst, typically made of vanadium pentoxide (V2O5), supported on a substrate like silica. The catalyst promotes the oxidation of sulfur dioxide to form sulfur trioxide (SO3).
2 SO2 + O2 ⇌ 2 SO3
3. Sulfur Trioxide Absorption: Sulfur trioxide exhibits high chemical reactivity and cannot be isolated as a pure gas directly. Instead, it is rapidly absorbed into a concentrated solution of sulfuric acid (H2SO4), forming oleum (H2S2O7) or pyrosulfuric acid. The reaction with sulfuric acid acts as a chemical sink, preventing the reverse reaction to convert sulfur trioxide back into sulfur dioxide.
SO3 + H2SO4 → H2S2O7
4. Dilution and Formation of Sulfuric Acid: Once oleum is created, it must be diluted in water in order to create concentrated sulfuric (H2SO4) acidity.
H2S2O7 + H2O → 2 H2SO4
The Contact Process is a continuous and cyclical process, where the unreacted sulfur dioxide, nitrogen oxides, and some sulfur trioxide are recycled back to the process to ensure a high conversion rate and efficiency.
Advantages of the Contact Process over the Lead Chamber Process include higher sulfur dioxide conversion efficiency, the ability to produce more concentrated sulfuric acid, and reduced environmental impact due to the absence of nitrogen oxide emissions. This process is key in the production of sulfuric acid. It finds use across many industries including chemical production and fertilizer manufacture.
Comparison between Lead Chamber and Contact Process
Compare and Contrast Lead Chamber Process with Contact Process for Producing Sulfuric Acid:
1. Efficiency of Sulfur Dioxide Conversion:
- Lead Chamber Process: The sulfur dioxide (SO2) conversion efficiency in the Lead Chamber Process is relatively low, typically ranging from 30% toThe Lead Chamber Process typically achieves only 30-70% sulfur dioxide conversion efficiency. Due to this mismanagement, yields decline substantially while waste emissions increase substantially and too much sulfur dioxide remains unsulfured and unconverted into sulfuric acid.
- Contact Process: The Contact Process achieves a much higher sulfur dioxide conversion efficiency, usually over 98%. This high conversion rate results in more effective utilization of sulfur dioxide and increased sulfuric acid production per unit of sulfur dioxide input.
2. Plant Capacity and Scalability:
- Lead Chamber Process: The Lead Chamber Process has limitations on plant capacity due to the relatively slow reaction rates and lower conversion efficiency. Large-scale production of sulfuric acid using this process is challenging and requires a considerable amount of space for the lead-lined chambers.
- Contact Process: The Contact Process is highly scalable and allows for the construction of larger production facilities. The higher conversion efficiency and faster reaction rates make it suitable for meeting the increasing demand for sulfuric acid in various industrial applications.
3. Environmental Impact:
- Lead Chamber Process: Lead Chamber Process involves emitting NOx into the atmosphere through chemical reactions involving either nitric dioxide or nitrous oxide. Nitrogen oxides pose serious threats to human health and the environment.
- Contact Process: The Contact Process does not produce nitrogen oxides as a byproduct, resulting in a lower environmental impact and reduced air pollution. This makes the Contact Process more environmentally friendly compared to the Lead Chamber Process.
4. Equipment and Operational Complexity:
- Lead Chamber Process: The Lead Chamber Process involves relatively simple equipment, mainly consisting of lead-lined chambers and absorption towers. However, the continuous operation and maintenance of these chambers can be challenging, especially in large-scale production plants.
- Contact Process: The Contact Process requires more complex equipment, including specialized reactors, heat exchangers, and a catalyst bed. The addition of a catalyst to any process adds another level of complexity and may exacerbate problems further down the road. Modern engineering and technology have made the operation and control of the Contact Process manageable and efficient.
5. Cost Considerations:
- Lead Chamber Process: The Lead Chamber Process benefits from using relatively cheap raw materials like elemental sulfur and does not require expensive catalysts. Its lower efficiency and higher waste emissions can lead to higher overall production costs.
- Contact Process: The Contact Process may involve higher initial investment costs due to the need for catalysts and more complex equipment. However, the high conversion efficiency and lower waste emissions contribute to overall cost-effectiveness and long-term savings.
6. Historical Significance:
- Lead Chamber Process: Lead Chamber Process was an influential event in history; it represented the first commercially viable method to produce sulfuric acid commercially and saw wide use during the 18th-century production of that compound.
- Contact Process: The Contact Process replaced the Lead Chamber Process as the dominant method for sulfuric acid production in modern times due to its higher efficiency and environmental benefits.
The Contact Process is the preferred method for sulfuric acid production in modern industries due to its higher efficiency, scalability, lower environmental impact, and cost-effectiveness compared to the traditional Lead Chamber Process.
Environmental Impact of the Lead Chamber Process and the Contact Process
The Lead Chamber Process and the Contact Process have different environmental impacts due to their distinct chemical reactions and operational characteristics.
Environmental Impact of the Lead Chamber Process:
1. Emission of Nitrogen Oxides (NOx): Environmental concerns with the Lead Chamber Process center on its potential release of nitrogen oxides (NOx). This gas results from the catalytic combustion of sulfur dioxide and contributes to air pollution. Acid rain poses a severe threat to soils, water bodies, ecosystems, and human health.
2. Sulfur Dioxide (SO2) Emissions: The Lead Chamber Process also emits unreacted sulfur dioxide (SO2) as a byproduct. SO2 (sulfur oxide) pollution has an adverse impact on respiratory systems and contributes to other forms of pollution like smog, particulate matter, and other air pollutants.
3. Limited Conversion Efficiency: The lower sulfur dioxide conversion efficiency of the Lead Chamber Process leads to larger quantities of unreacted sulfur dioxide and nitrogen oxides being released into the atmosphere, further exacerbating air pollution issues.
Environmental Impact of the Contact Process:
1. Reduced Nitrogen Oxides Emissions: Unlike the Lead Chamber Process, the Contact Process does not produce nitrogen oxides as byproducts. The absence of NOx emissions significantly reduces its impact on air quality and mitigates the potential for acid rain formation.
2. Sulfur Dioxide Emissions: While the Contact Process does produce sulfur dioxide as an intermediate, modern plants are equipped with advanced gas scrubbing technologies to capture and remove most of the sulfur dioxide before it is released into the atmosphere. These technologies help reduce the environmental impact associated with sulfur dioxide emissions.
3. Catalyst and Energy Consumption: The Contact Process requires a catalyst, typically vanadium pentoxide, which might have environmental implications during its production and disposal. Additionally, the process operates at higher temperatures and pressures, requiring more energy input compared to the Lead Chamber Process.
The Contact Process is considered more environmentally friendly compared to the Lead Chamber Process, mainly due to its higher sulfur dioxide conversion efficiency, reduced emissions of nitrogen oxides, and the ability to incorporate pollution control measures. Proper management and regulation is required in order to minimize the effect of both processes on air and water resources.
In modern industrial practices, the Contact Process has become the preferred method for sulfuric acid production due to its superior efficiency and reduced environmental impact, highlighting the importance of adopting sustainable technologies to mitigate the environmental consequences of industrial processes.
Safety Measures in Sulfuric Acid Production
To safeguard workers, local communities, and the environment during sulfuric acid production (H2SO4) it is imperative that stringent safety precautions are taken.
Safety measures for sulfuric acid production:
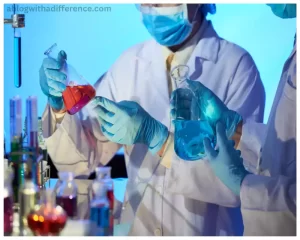
1. Personal Protective Equipment (PPE): When producing sulfuric acid, chemical-resistant clothing and protective gear must be worn to safeguard workers against chemical burns. PPE helps protect against accidental splashes, spills, and inhalation of acid vapors.
2. Engineering Controls: Implement engineering controls to minimize the risk of exposure to sulfuric acid. This may include the installation of closed systems and automated processes to reduce manual handling and the use of chemical fume hoods or ventilation systems to control acid vapors.
3. Training and Education: Workers should receive education and training on the risks posed by sulfuric acid and proper handling techniques, emergency response protocols and equipment needed for handling it properly. Regular refresher training should be conducted to reinforce safe practices.
4. Emergency Preparedness: Develop and communicate clear emergency response plans in the event of spills, leaks, or other accidents. Provide workers with the knowledge and tools to respond quickly and effectively to mitigate potential hazards.
5. Chemical Storage: Store sulfuric acid in designated, well-ventilated areas away from incompatible substances. Ensure proper labeling of containers, and keep them securely closed when not in use to prevent accidental spills.
6. Spill Containment and Cleanup: Have appropriate spill containment materials readily available to respond to spills promptly. Establish procedures for the safe cleanup and disposal of spilled sulfuric acid, following regulatory guidelines.
7. Corrosion-resistant Equipment: When working with equipment that comes into contact with sulfuric acids, use corrosion-resistant materials such as stainless steel, glass or certain plastics to make contact easier and extend equipment longevity. Regularly inspect and maintain equipment to detect and address potential leaks or weaknesses.
8. Safe Handling Procedures: Follow safe handling procedures, such as slow and controlled addition of sulfuric acid to other substances to avoid splashes or violent reactions. Always add acid to water (not the other way around) when diluting concentrated sulfuric acid to reduce the risk of sudden heat generation.
9. Contingency Plans: Develop contingency plans for equipment failure, power outages, and other unexpected events to ensure safe shutdown procedures and prevent hazardous situations.
10. Regulatory Compliance: Adhere to all safety and environmental regulations related to producing, storing and transporting sulfuric acids. Regularly review and update safety practices to align with the latest industry standards.
By implementing these safety measures, sulfuric acid production facilities can significantly reduce the risks associated with handling this hazardous chemical and create a safer working environment for employees and the surrounding community.
Industrial Applications of Sulfuric Acid
Sulfuric acid (H2SO4) finds extensive application within industry. Due to its acidity and reactivity, this compound plays an integral part in many processes and products. Sulfuric acid has many industrial applications.
1. Chemical Production: Sulfuric Acid is widely utilized for production of dyes, synthetic resins pigments and other chemical-related products. It serves as a key raw material or catalyst in many chemical reactions.
2. Fertilizer Production: Fertiliser production such as ammonium and superphosphate requires sulfuric acid for production. These fertilizers provide essential nutrients like phosphorous to enhance plant growth.
3. Petroleum Refining: At petroleum refineries, sulfuric acid is utilized to produce high-octane gas while eliminating impurities like sulfur and nitrogen from petroleum products.
4. Metal Processing: Sulfuric acid is utilized in various metal processing applications, including pickling and electroplating. It is used to clean and remove oxide layers from metal surfaces before further processing or finishing.
5. Rayon and Textile Industry: Sulfuric acid is employed in the manufacturing of rayon fibers and as a dyeing and finishing agent in the textile industry.
6. Battery Manufacturing: Lead-acid batteries, commonly found in automobiles and other applications, utilize sulfuric acid as the chemical catalyst that facilitates energy-producing reactions within them.
7. Water Treatment: Sulfuric acid can often be seen used to balance alkaline water supplies by neutralizing its pH value or altering it accordingly. Utilizing this product in wastewater treatment helps remove heavy metals and impurities.
8. Cleaning Agents: Due to its strong acidic properties, sulfuric acid is used in various cleaning and degreasing applications for industrial equipment and surfaces.
9. Explosives Manufacturing: Sulfuric Acid is an integral part of explosives such as TNT and Nitroglycerin.
10. Paper and Pulp Industry: Sulfuric acid is widely utilized within the paper manufacturing and pulping process to remove lignin.
11. Synthetic Rubber Production: Sulfuric acid is widely employed for producing synthetic rubber such as Styrene Butadiene Rubber (SBR).
12. Food Industry: Sulfuric acid is used as a pH regulator and acidulant in the food industry for certain food products, like beverages and canned goods.
Sulfuric acid can be highly hazardous, necessitating special handling procedures for safe use and management.
Conclusion
Sulfuric Acid (H2SO4) serves a multitude of industrial uses and remains an indispensable chemical compound. Its strong acidity and reactivity make it an essential component in various processes and products across different industries.
The Lead Chamber Process, historically significant as the first commercial method for sulfuric acid production, was later replaced by the more efficient Contact Process. The Contact Process has become the dominant method due to its higher efficiency, greater plant capacity, reduced environmental impact, and economic advantages in modern industrial settings.
Sulfuric Acid has many applications within industries including chemical production, fertilizer manufacture, petroleum refining and metal processing. Utilized for producing synthetic resins, pigments, pharmaceutical products, etc. Sulfuric acid is used in petroleum refining, metal processing, rayon and textile industries, battery manufacturing, water treatment, cleaning agents, explosives production, paper, and pulp industry, synthetic rubber production, and as a pH regulator in the food industry.