Hastelloy and Stainless steel are two widely used materials with distinct properties and applications. This article aims to shed light on the differences between Hastelloy and stainless steel, their unique characteristics, and the industries where they find their most significant utility.
What is Hastelloy?
Hastelloy alloys are high-performance materials known for their exceptional corrosion resistance, high-temperature stability, and superior mechanical characteristics. Made up mainly of nickel, chrome, and molybdenum elements – along with others that give these alloys their special properties.
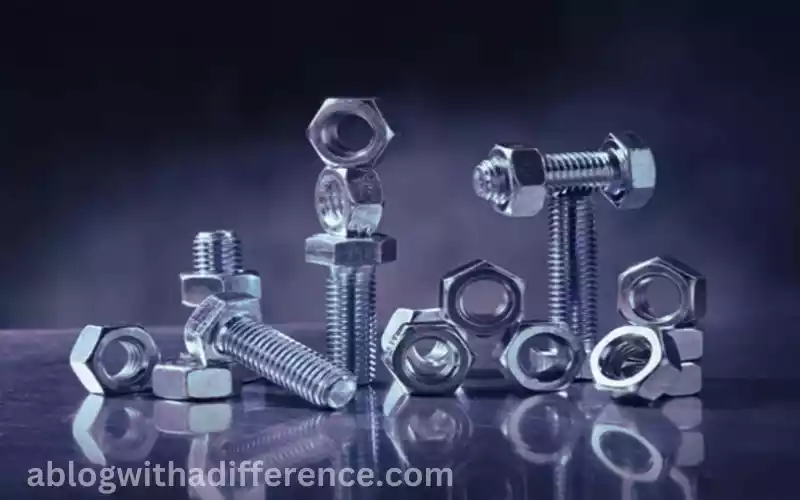
Hastelloys offer great advantages to industries demanding corrosion-proof components in products designed to withstand demanding environments such as shipyard environments. Hastelloy alloys are widely used in various industries where resistance to harsh environments and aggressive chemicals is essential.
The development of Hastelloy dates back to the early 20th century when it was first created by Haynes International, Inc. The name “Hastelloy” is actually a trademark of Haynes International, and different grades of Hastelloy have been developed over the years to meet specific application requirements.
Some of the key properties and features of Hastelloy alloys include:
- Corrosion Resistance: Hastelloy alloys offer outstanding resistance to corrosion in highly corrosive environments, including acids, alkalis, and chlorides. They are particularly effective in resisting localized corrosion and stress corrosion cracking.
- High-Temperature Stability: Hastelloy alloys retain their strength and integrity even at elevated temperatures. They exhibit excellent resistance to oxidation and other high-temperature degradation mechanisms.
- Mechanical Properties: Hastelloy alloys possess excellent mechanical strength and toughness, making them suitable for demanding applications that require both corrosion resistance and structural integrity.
- Versatility: Hastelloy alloys come in various grades, each designed for specific applications and industries. This versatility allows engineers and designers to choose the most suitable alloy for their particular needs.
- Applications: Hastelloy finds extensive use in industries such as chemical processing, petrochemical, aerospace, marine, pharmaceutical, and nuclear industries, among others. It is commonly employed in reactors, heat exchangers, valves, piping systems, and other critical components exposed to aggressive environments.
- Weldability and Fabricability: While Hastelloy alloys can be more challenging to weld and fabricate compared to stainless steel, specialized welding techniques and equipment can overcome these challenges to produce high-quality components.
Hastelloy is a preferred choice in industries where corrosion resistance and high-temperature performance are crucial. The specific grade of Hastelloy chosen for an application will depend on the exact conditions it will be exposed to and the required performance characteristics.
Applications of Hastelloy
Hastelloy’s exceptional corrosion resistance, high-temperature stability, and superior mechanical properties make it highly suitable for a wide range of applications in various industries.
Some of the key applications of Hastelloy include:
- Chemical Processing: Hastelloy is extensively used in chemical processing industries, including petrochemical plants, chemical reactors, and pharmaceutical facilities. Its resistance to corrosive chemicals such as acids (sulfuric acid, hydrochloric acid, nitric acid), alkaline solutions, and chlorides makes it ideal for handling aggressive media.
- Aerospace and Aviation: Hastelloy is utilized in aerospace and aviation applications due to its ability to withstand high-temperature environments, oxidation resistance, and corrosion resistance in jet engines, combustion chambers, and exhaust systems.
- Oil and Gas: In the oil and gas industry, Hastelloy is used for downhole equipment, wellhead components, and pipelines, where exposure to corrosive fluids and high-pressure conditions is common.
- Marine and Offshore: Hastelloy is employed in marine and offshore applications, including seawater handling systems, desalination plants, and offshore drilling platforms, where it resists corrosion from saline environments.
- Nuclear Power: Hastelloy is favored in the nuclear power industry for its resistance to radiation and corrosion in nuclear reactors and related components.
- Pollution Control: Hastelloy is used in pollution control equipment, such as scrubbers and exhaust systems, where it helps resist acidic and corrosive emissions.
- Pulp and Paper: The pulp and paper industry utilizes Hastelloy in chemical processing equipment, digesters, and bleach plants due to its resistance to corrosive chemicals used in the paper-making process.
- Pharmaceuticals: In pharmaceutical manufacturing, Hastelloy is employed in reaction vessels and equipment that handle aggressive chemicals and high-temperature processes.
- Heat Exchangers: Hastelloy is used in heat exchangers for its excellent corrosion resistance and heat transfer properties, making it suitable for a wide range of industrial heat transfer applications.
- Food and Beverage: Certain grades of Hastelloy are used in food and beverage processing equipment, where resistance to acids and other corrosive substances is required for hygienic and sanitary conditions.
- Electronics and Semiconductors: Hastelloy is utilized in electronics and semiconductor manufacturing for its resistance to acidic and alkaline chemical solutions used in etching processes.
- Automotive: Some high-performance automotive components, such as exhaust systems and catalytic converters, use Hastelloy due to its high-temperature stability and corrosion resistance.
- Springs and Fasteners: Hastelloy is employed in springs, fasteners, and other critical components that require both high strength and corrosion resistance.
These are just a few examples of the diverse applications of Hastelloy. The selection of the appropriate grade of Hastelloy for a specific application depends on the environmental conditions, temperature range, and specific chemical exposures it will encounter. Each grade of Hastelloy is designed to excel in particular conditions, providing engineers and designers with a wide range of options for their respective industries.
What is Stainless Steel?
An alloy classified as stainless steel contains at least 10.5% chromium by mass and must have at least 10.5% in terms of mass as chromium is essential in creating the passive film, an oxide passive layer on its surface that serves to protect it against corrosion, while giving stainless steel its unique identity and distinctive look.
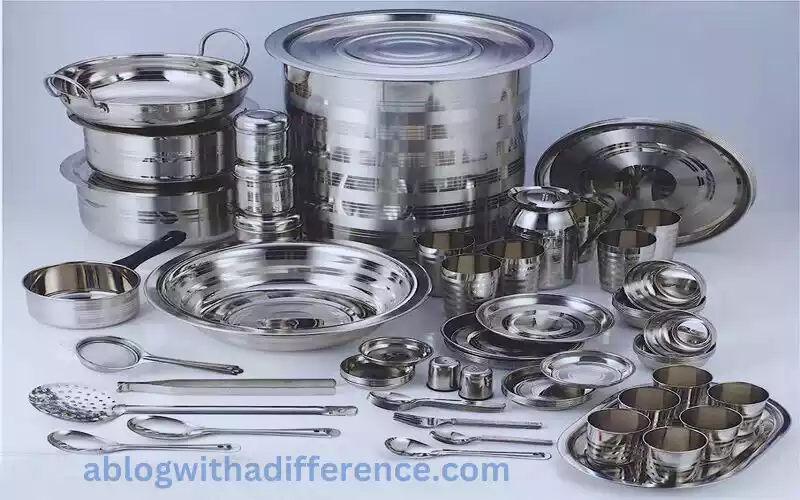
A passive film protects steel beneath from both oxidation and corrosion by serving as a barrier that provides additional resistance from further attack from outside sources.
Stainless steel boasts many properties which make it suitable for various industrial uses and applications, and boast numerous.
Key characteristics and features that set it apart from its alternatives:
- Corrosion Resistant: One of Stainless Steel’s primary advantages lies in its corrosion-resistance. This makes it suitable for environments containing moisture, humidity and other corrosive materials as it won’t rust or stain easily.
- Alloying Elements: Stainless steel may contain alloying elements like nickel, molybdenum or titanium to improve properties such as corrosion resistance, strength and toughness. These additions enhance properties like corrosion resistance.
- Different Grades: Stainless steel comes in various grades and classifications that offer unique properties suited for specific uses and applications. Popular options for stainless steel grades are austenitic, ferritic, martensitic duplex stainless and precipitation hardening steels.
- Strength and Durability: Stainless steel is widely acknowledged for its long-term strength and durability, being capable of withstanding both extreme high temperature environments as well as cold conditions without becoming compromised, making it the go-to material in applications which require stability across a broad temperature spectrum.
- Hygiene and Aesthetics: Stainless steel is easy to keep clean, nonporous and resistant to bacteria growth – characteristics which make it the ideal material choice for applications requiring high levels of hygiene, such as those found within medical and food industries. Additionally, it has a bright and clean appearance that can enhance the aesthetic appeal of products and structures.
- Ductility and Formability: Stainless steel can be easily formed and fabricated into various shapes, allowing for a wide range of design possibilities. It is ductile, which means it can be stretched and drawn without breaking, making it suitable for various manufacturing processes.
- Recyclability: Stainless steel is highly recyclable, and it retains its properties through recycling processes, making it an environmentally friendly material choice.
Due to its combination of exceptional properties, stainless is used in numerous applications ranging from kitchen utensils and appliances, cutlery, automobile parts, construction materials for architectural structures, medical equipment and chemical processing machinery, among many other uses. When selecting grades depending upon an application – which include corrosion resistance, strength and formability requirements.
Applications of Stainless Steel
Due to stainless steel’s versatility, resistance to corrosion, and superior mechanical properties it finds wide application in numerous industries and applications.
Some of the key applications of stainless steel include:
- Kitchen Appliances: Stainless steel surfaces are widely utilized in appliances like refrigerators, microwaves ovens and dishwashers.
- Cutlery and Cookware: Stainless steel has become widely popular as the material of choice for cutlery production (knives forks spoons) as well as cookware production (pots and pans), due to its superior corrosion resistance and durability.
- Architecture and Construction: Stainless steel has long been utilized in architecture and construction applications handrails and facades, due to its corrosion-resistance. Due to these characteristics, it is an attractive material choice.
- Automotive Industry: Stainless Steel has become an invaluable material in automotive exhaust systems, grilles and trims due to its exceptional heat performance and corrosion-resistance properties.
- Medical Devices: Stainless Steel has long been utilized as a biocompatible material in medical device production and implant manufacturing.
- Aerospace and Aviation: Stainless steel has become widely utilized within both sectors due to its corrosion-resistance, strength-to-weight ratio and lightweight characteristics. Stainless Steel components used within aerospace include structural parts, fittings and fasteners due to its corrosion protection properties and strength-to-weight ratio.
- Marine and Offshore: Stainless Steel has long been utilized for marine and off-shore uses, from boat fittings and ship construction, to making an effective offshore platform due to its corrosion resistant qualities.
- Food and Beverage Processing: Stainless Steel has become widely utilized within the food and drink industries to construct tanks, pipes and processing equipment due to its corrosion-resistant and hygienic qualities.
- Pharmaceutical Industry: Stainless steel is often employed by the pharmaceutical industry as storage vessels, pipes and processing equipment that requires high hygiene levels and corrosion-resistance for its operation.
- Chemical and Petrochemical: Stainless steel equipment such as tanks and reactors is frequently found in chemical and petroleum plants that deal with highly corrosive materials and high temperature processes.
- Water and Wastewater treatment: Due to its resistance to corrosion, stainless steel has long been chosen for water treatment facility pipes, pumps, and valves made up of water treatment facility pipes, pumps and valves.
- Energy and Power Production: Power plants often feature stainless steel components like heat exchangers and boilers in order to increase power production.
- Furniture and Home Decor: Due to its aesthetic appeal and modern appearance, stainless steel has long been used as the material of choice in furniture and home decoration items.
- Electronics and Communication: Due to its excellent electrical conductivity, stainless steel has long been utilized as the material of choice in electronic enclosures, communications equipment and electrical appliances.
- Industrial Equipment: Stainless Steel is widely utilized for industrial equipment due to its strength and resistance against harsh environments.
Corrosion resistance, strength and temperature resistance are just three considerations when selecting an appropriate grade of stainless.
Comparing Hastelloy and Stainless Steel
Hastelloy and stainless steel are both important materials with distinct properties and applications.
Here’s a comparative analysis of these two materials:
- Composition:
- Hastelloy: Hastelloy is a group of alloys primarily composed of nickel, chromium, molybdenum, and other elements like iron, tungsten, and cobalt. The specific composition varies depending on the grade of Hastelloy.
- Stainless Steel: Stainless steel is a steel alloy that contains a minimum of 10.5% chromium by mass. It also often includes other elements such as nickel, molybdenum, and titanium, depending on the specific grade.
- Corrosion Resistance:
- Hastelloy: Hastelloy is renowned for its exceptional corrosion resistance in highly corrosive environments, such as acidic, alkaline, and chloride-rich conditions. It surpasses many stainless steel grades in corrosive resistance.
- Stainless Steel: Stainless steel is also corrosion-resistant, but the level of resistance varies depending on the specific grade. It is commonly used for its general corrosion resistance, especially in mildly corrosive environments.
- High-Temperature Performance:
- Hastelloy: Hastelloy is highly stable and maintains its strength even at elevated temperatures, making it suitable for high-temperature applications such as in the aerospace and chemical industries.
- Stainless Steel: While stainless steel also exhibits good high-temperature performance, it may not match the exceptional capabilities of certain Hastelloy grades in extreme temperature environments.
- Mechanical Properties:
- Hastelloy: Hastelloy offers excellent mechanical properties, including high tensile strength and toughness. It is often chosen for critical applications where both corrosion resistance and mechanical strength are essential.
- Stainless Steel: Stainless steel is renowned for its strength and durability. Different grades exhibit varying mechanical properties, allowing for a wide range of applications.
- Cost:
- Hastelloy: Hastelloy is generally more expensive than stainless steel due to its complex composition, which includes higher amounts of expensive elements like nickel and molybdenum.
- Stainless Steel: Stainless steel is generally more cost-effective compared to Hastelloy, making it a popular choice for a wide range of applications.
- Weldability and Fabrication:
- Hastelloy: Hastelloy can be more challenging to weld and fabricate compared to stainless steel. Specialized welding techniques and equipment may be required for certain Hastelloy grades.
- Stainless Steel: Stainless steel is relatively easy to weld and fabricate, making it more accessible for many manufacturing processes.
- Applications:
- Hastelloy: Hastelloy is commonly used in industries that require superior corrosion resistance and high-temperature performance, such as chemical processing, aerospace, and marine applications.
- Stainless Steel: Stainless steel finds widespread use in various industries, including kitchen appliances, architecture, automotive, medical, and food processing, where corrosion resistance and durability are needed.
Hastelloy excels in extreme environments with aggressive chemicals and high temperatures, while stainless steel offers a cost-effective solution with good corrosion resistance and strength for a wide range of applications. The choice between Hastelloy and stainless steel depends on the specific requirements and conditions of each application.
Similarities of Hastelloy and Stainless Steel
Hastelloy and stainless steel, despite their differences, also share some similarities, which contribute to their widespread use in various industries.
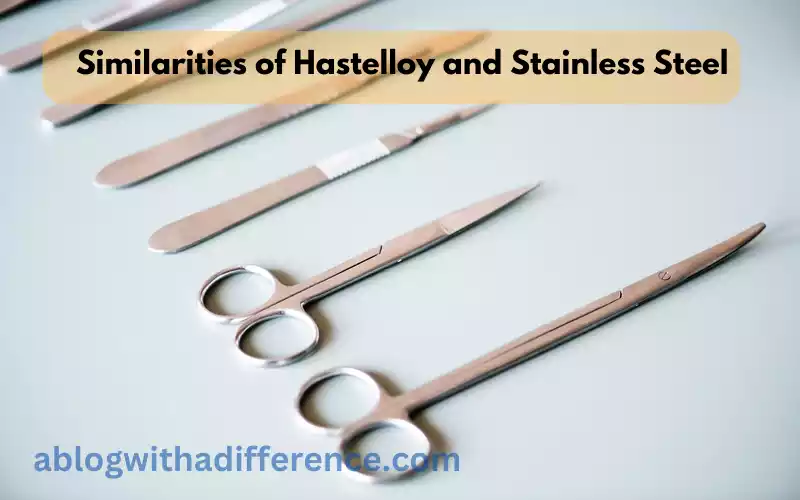
Here are the key similarities between Hastelloy and stainless steel:
- Corrosion Resistance: Both Hastelloy and stainless steel are renowned for their corrosion-resistant properties. While Hastelloy exhibits exceptional resistance to a wide range of corrosive environments, stainless steel also provides good resistance to corrosion, making both materials suitable for applications exposed to harsh conditions.
- Strength and Durability: Both materials possess remarkable mechanical properties, with high tensile strengths and durability being particular standouts. They can withstand mechanical stresses and loads, ensuring long-lasting performance in different applications.
- Versatility: Both Hastelloy and stainless steel come in various grades and compositions, each tailored to meet specific application requirements. This versatility allows for a wide range of options to address different industrial needs.
- Wide Range of Applications: Both materials find applications in numerous industries due to their unique properties. Hastelloy is commonly used in chemical processing, aerospace, and marine industries, while stainless steel has diverse uses in architecture, automotive, medical, and food processing sectors, among others.
- Recyclability: Both Hastelloy and stainless steel are recyclable materials, contributing to sustainable practices and reducing the demand for virgin resources.
- Fabricability: While Hastelloy may require more specialized welding techniques and fabrication processes compared to stainless steel, both materials are amenable to various manufacturing techniques, making them accessible for a wide range of industrial processes.
- Longevity: Due to their corrosion resistance and durable properties, both Hastelloy and stainless steel offer long service life, reducing the need for frequent replacements and thus minimizing waste.
- Hygiene: Both materials are non-porous and easy to clean, making them suitable for applications where hygiene is essential, such as food processing, pharmaceutical, and medical industries.
- Resistance to High Temperatures: Both Hastelloy and certain stainless steel grades can withstand elevated temperatures, making them suitable for high-temperature applications, such as aerospace, chemical processing, and power generation.
While Hastelloy and stainless steel may differ significantly in terms of composition, cost, and specific applications, their shared characteristics make them valuable choices for various industries where corrosion resistance, strength, and durability are essential requirements. Selecting the most appropriate material between the two depends on the specific needs and conditions of each application.
Environmental Impact
The environmental impact of both Hastelloy and Stainless steel can vary based on several factors, including their production processes, raw material sourcing, use, and end-of-life considerations.
- Production Processes:
- Hastelloy: The production of Hastelloy involves extracting and processing raw materials like nickel, chromium, and other elements, which can have environmental impacts if not managed responsibly. The refining and alloying processes can consume significant amounts of energy and generate greenhouse gas emissions.
- Stainless Steel: Stainless steel production also involves mining and processing raw materials like iron ore and chromium, contributing to energy consumption and emissions. Advancements in production technologies have led to more efficient processes, reducing environmental impacts over time.
- Raw Material Sourcing:
- Hastelloy: Some elements used in Hastelloy, such as nickel, are not as abundant as iron, which is a primary component of stainless steel. Nickel mining can have environmental consequences, including habitat destruction and water pollution.
- Stainless Steel: Stainless steel relies heavily on iron, which is one of the most abundant metals on Earth. Mining iron ore can still have environmental impacts, particularly if not conducted responsibly.
- Recycling and Recyclability:
- Hastelloy: Hastelloy is recyclable, and its recycling rate is steadily increasing. Due to its relatively small market compared to stainless steel, recycling infrastructure may not be as developed.
- Stainless Steel: Stainless steel is highly recyclable, and it is one of the most recycled materials globally. Its high recyclability contributes to reducing its environmental impact and conserving resources.
- End-of-Life Considerations:
- Hastelloy: When Hastelloy products reach the end of their useful life, proper recycling or disposal is essential to avoid environmental harm. If not recycled, Hastelloy items could contribute to waste streams and landfill usage.
- Stainless Steel: Stainless steel’s high recyclability ensures that it can be repurposed into new products after its initial use, reducing the need for virgin material and lowering the environmental impact.
- Energy Efficiency and Durability:
- Hastelloy: The durability and resistance to corrosion and degradation of Hastelloy can extend the lifespan of products made from this material. Longer-lasting products reduce the need for frequent replacements, positively impacting the environment.
- Stainless Steel: Stainless steel’s durability and longevity also contribute to its environmental benefits, as durable products reduce waste and conserve resources.
Both Hastelloy and stainless steel have environmental impacts related to their production, raw material sourcing, use, and end-of-life considerations.
While stainless steel’s wide adoption and recycling infrastructure have led to a more established sustainable approach, Hastelloy’s specific applications and smaller market may require continued efforts to improve its environmental performance through responsible sourcing, recycling, and waste management practices.
As with any material, considering factors like responsible sourcing, efficient production methods, recycling, and product durability are crucial to minimizing the environmental impact of both Hastelloy and stainless steel.
Choosing the Right Material
Finding the appropriate material to meet a given application depends upon many different considerations and parameters.
Here are a few steps that will assist with material selection:
- Identify Application Requirements:
- Determine the specific requirements of the application, including environmental conditions (temperature, humidity, corrosive substances), mechanical loads, and any regulatory or industry standards that must be met.
- Performance Characteristics:
- Consider the essential performance characteristics needed for the application, such as corrosion resistance, mechanical strength, thermal stability, electrical conductivity, or other specific properties.
- Material Properties Comparison:
- Compare the properties of different materials (e.g., Hastelloy, stainless steel, other alloys, or non-metallic materials) to identify which ones align best with the required performance characteristics.
- Cost Considerations:
- Evaluate the cost implications of using different materials, including initial material costs, manufacturing costs, maintenance, and potential replacement costs over the product’s lifecycle.
- Availability and Supply Chain:
- Assess the availability of the chosen material and the reliability of its supply chain to ensure consistent access to the required materials.
- Environmental Impact:
- Consider the environmental impact of the material, including its production, recycling potential, and its overall sustainability compared to alternatives.
- Industry Standards and Codes:
- Check if there are any industry-specific standards, codes, or certifications that dictate the use of certain materials for the application.
- Experience and Expertise:
- Consider the experience and expertise of the team or organization in working with specific materials. Familiarity with a material can impact fabrication, welding, and maintenance processes.
- Material Compatibility:
- Ensure that the selected material is compatible with other materials or substances it will come into contact with during its use to prevent potential chemical reactions or degradation.
- Future Requirements:
- Anticipate any potential changes or future requirements that may impact the material’s suitability over time, such as increased loads, temperature variations, or environmental regulations.
- Risk Assessment:
- Conduct a risk assessment to evaluate potential risks associated with the material choice and how they can be mitigated.
- Consultation and Collaboration:
- Engage with materials experts, engineers, suppliers, or consultants who have experience in selecting materials for similar applications.
Following these steps and conducting a careful analysis will enable you to make an informed decision regarding the ideal material for your application. Consider performance, cost and availability alongside sustainability and any possible risks when making this choice.
Conclusion
The choice between Hastelloy and stainless steel hinges on the specific requirements and conditions of the application. Both materials offer unique properties that cater to different industrial needs.
Hastelloy, with its exceptional corrosion resistance and high-temperature stability, excels in aggressive and extreme environments, such as chemical processing, aerospace, and nuclear applications. Its mechanical strength and toughness make it suitable for critical components in harsh conditions. Its higher cost and potential fabrication challenges may be a consideration for certain projects.